Sekrety projektowania elastycznych PCB: Co musisz wiedzieć? – na to pytanie odpowiada Konrad Bruliński z Lemontech
W erze postępującej miniaturyzacji oraz wzrastającego zapotrzebowania na urządzenia lekkie, trwałe i elastyczne, tradycyjne obwody drukowane wykonane na laminacie FR4 coraz częściej okazują się niewystarczające pod kątem mechanicznego dopasowania do obudowy. Nowoczesne konstrukcje elektroniczne wymagają integracji funkcjonalności z elastycznością mechaniczną, co prowadzi do rosnącej popularności technologii PCB Flex oraz Rigid-Flex.
Elastyczne PCB (Flex) oraz sztywno-giętkie obwody drukowane (Rigid-Flex) umożliwiają projektowanie urządzeń, które są bardziej kompaktowe, odporne na trudne warunki środowiskowe i zdolne do pracy w aplikacjach wymagających ruchomych elementów. Dzięki swojej zdolności do pracy w trójwymiarowej przestrzeni otwierają nowe możliwości w projektowaniu produktów, których celem jest zrównoważenie innowacyjności, wydajności i trwałości.
Projektowanie tych obwodów wymaga jednak nie tylko znajomości podstawowych zasad tworzenia tradycyjnych PCB, ale również głębokiego zrozumienia specyfiki elastycznych materiałów, wymagań mechanicznych oraz szczegółowych procesów produkcyjnych. Zarówno projektanci, jak i inżynierowie muszą zmierzyć się z wyzwaniami, takimi jak naprężenia mechaniczne, odpowiednie rozmieszczenie komponentów oraz zapewnienie trwałości w warunkach dynamicznych.
W niniejszym artykule przyjrzymy się, czym dokładnie są PCB Flex i Rigid-Flex, jakie są ich zalety i zastosowania, a także jakie kroki należy podjąć, by skutecznie zaprojektować takie rozwiązania. Omówimy również kluczowe wyzwania, które mogą pojawić się w trakcie projektowania i produkcji oraz sposoby ich pokonania. Zrozumienie tej technologii otwiera drzwi do bardziej zaawansowanych, a zarazem bardziej dostosowanych do współczesnych wymagań, projektów elektronicznych.
Główna różnica między PCB Flex a PCB Rigid-Flex tkwi w ich konstrukcji i zastosowaniach:
- PCB Flex to wyłącznie elastyczne obwody drukowane, które są w pełni wykonane z elastycznych materiałów, takich jak poliamid. Dzięki temu mogą być dowolnie wyginane i formowane, co czyni je idealnym rozwiązaniem dla aplikacji wymagających ruchu lub dostosowania do nietypowych kształtów;
- PCB Rigid-Flex natomiast to hybryda, która łączy sekcje elastyczne (flex) z sztywnymi (rigid). Sekcje sztywne umożliwiają montaż i trwałe podtrzymanie bardziej wymagających komponentów elektronicznych, takich jak duże złącza czy procesory, podczas gdy sekcje elastyczne pozwalają na gięcie i adaptację obwodu do złożonych przestrzeni.
Podczas gdy PCB Flex są stosowane tam, gdzie wymagana jest maksymalna elastyczność, PCB Rigid-Flex są preferowane w projektach wymagających zarówno elastyczności, jak i mechanicznej stabilności w określonych punktach konstrukcji.
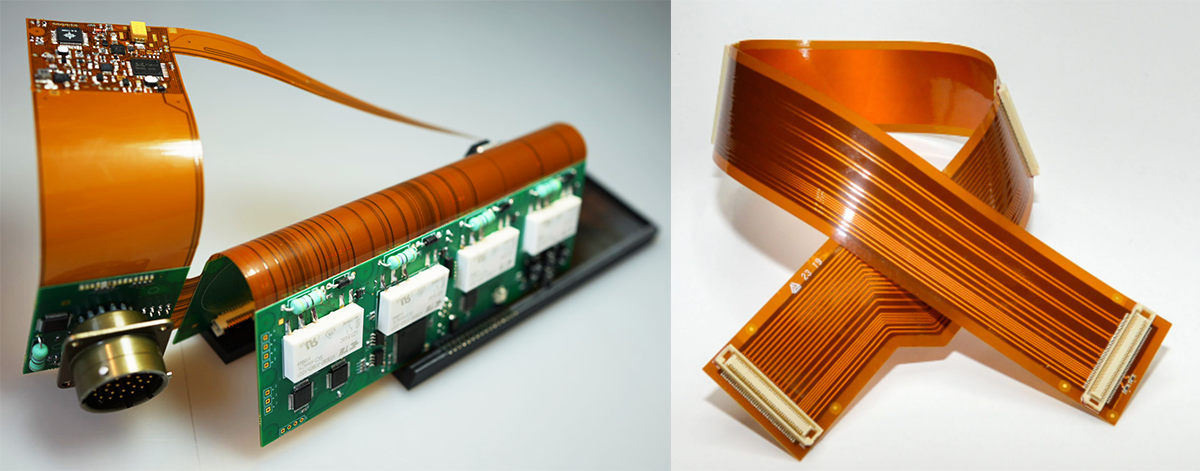
Po lewej PCB Rigit-Flex (źródło: Semicon sp. z o.o.), po prawej PCB Flex (źródło: Andwin Circuits PCB Expert)
Dodatkowo płytki elastyczne PCB flex powinniśmy podzielić na dwa główne typy w zależności od sposobu ich użytkowania: statyczne i dynamiczne:
- Flexy statyczne (ang. static flex PCB): Są projektowane z myślą o jednokrotnym ułożeniu w stałej pozycji. Po zamontowaniu nie są przeznaczone do ciągłego ruchu. Najczęściej stosuje się je w urządzeniach o ograniczonej przestrzeni, takich jak smartfony czy aparaty fotograficzne, gdzie kształt flexa jest dopasowany do wnętrza obudowy, ale sam obwód pozostaje nieruchomy podczas pracy. Dla tego typu laminatów wytrzymałość mechaniczna na zginanie wynosi ok. 100;
- Flexy dynamiczne (ang. dynamic flex PCB): Są przeznaczone do pracy w warunkach, gdzie dochodzi do ciągłego zginania i ruchu. W takich projektach kluczowe jest użycie materiałów o dużej elastyczności i odporności na zmęczenie, a także odpowiednie zaprojektowanie ścieżek i stref gięcia, aby wytrzymały setki tysięcy, a nawet miliony cykli zginania. Flexy dynamiczne znajdują zastosowanie w ruchomych elementach urządzeń, takich jak głowice drukarek, zawiasy laptopów czy systemy robotyczne. Dla tego typu laminatów wytrzymałość mechaniczna na zginanie wynosi dziesiątki tysięcy.
Jedym z kluczowych parametrów projektowych w przypadku flexów jest promień gięcia (ang. bend radius). Definiuje on minimalną krzywiznę, jaką można nadać elastycznemu obwodowi drukowanemu bez ryzyka uszkodzenia materiału lub ścieżek przewodzących. Promień gięcia jest kluczowym parametrem naszego obwodu ponieważ: zapobieganie pęknięciom (zbyt mały promień gięcia może prowadzić do pęknięcia materiału podłoża lub zerwania ścieżek przewodzących), trwałość (odpowiednio dobrany promień gięcia zwiększa wytrzymałość flexa na wielokrotne cykle zginania w dynamicznych aplikacjach) oraz niezawodność (minimalizacja naprężeń w strefach gięcia poprawia długoterminową niezawodność obwodu).
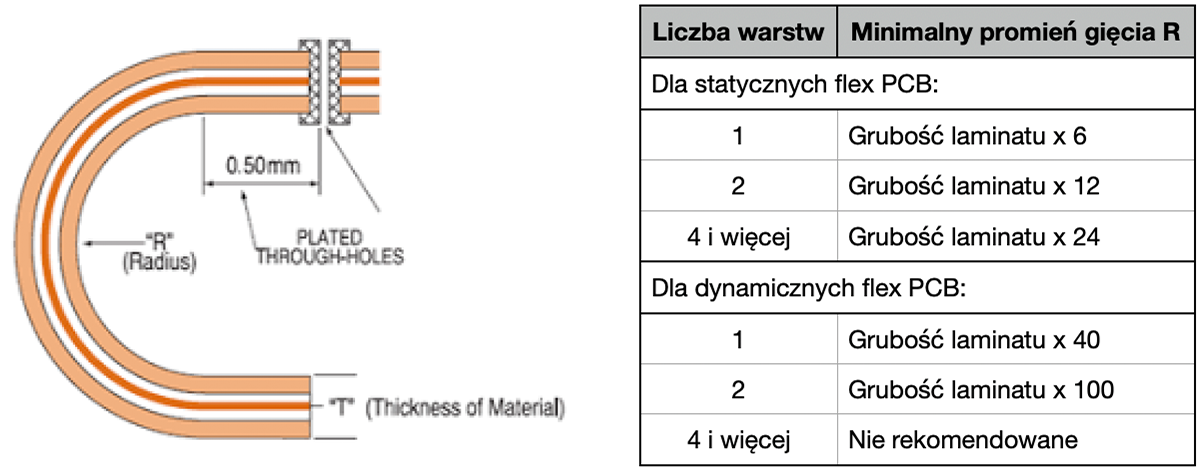
Źródło rysunku po lewej: FPCway
Czynniki wpływające na promień gięcia:
- Grubość materiału: Im cieńszy flex, tym mniejszy promień gięcia można zastosować;
- Liczba warstw: Więcej warstw zwiększa grubość i ogranicza elastyczność;
- Typ materiału: Poliamid jest bardziej odporny na naprężenia niż standardowe laminaty PCB;
- Układ ścieżek: Ścieżki powinny być prowadzone równolegle do kierunku gięcia, unikać ostrych kątów i przelotek w strefach gięcia;
- Osłony ochronne (coverlay): Grubość i elastyczność osłony wpływają na promień gięcia.
Ważne jest także zapewnienie odpowiedniej izolacji warstwy miedzi. W tym celu stosuje się osłony ochronne (coverlay), które zabezpieczają warstwę przed uszkodzeniami mechanicznymi i zwarciami. W strefach gięcia należy upewnić się, że używany materiał osłony jest wystarczająco elastyczny. Należy również unikać umieszczania przelotek lub otworów w strefach gięcia, ponieważ mogą one osłabić konstrukcję flexa.
Rozmieszczenie przelotek to kolejny istotny aspekt projektowania. Przelotki umieszczone w strefach gięcia są szczególnie narażone na uszkodzenia, dlatego należy ich unikać w tych miejscach. Jeżeli przelotki muszą znajdować się w strefie gięcia, powinny być odpowiednio wzmocnione za pomocą dodatkowych warstw ochronnych, takich jak coverlay, lub rozmieszczone w obszarach o najmniejszych naprężeniach.
Kolejnym aspektem podczas projektowania elastycznych obwodów jest Power Plane. Warstwa power plane dla obwodów flex wymaga uwzględnienia specyficznych właściwości elastycznych materiałów oraz warunków pracy, takich jak naprężenia mechaniczne i dynamiczne zginanie. W przeciwieństwie do sztywnych PCB, flex wymaga bardziej przemyślanego podejścia, aby zapewnić zarówno niezawodność elektryczną, jak i mechaniczną.
Kluczowe jest unikanie ciągłego pokrycia dużych obszarów miedzią. Duże powierzchnie miedzi zwiększają sztywność obwodu, co utrudnia jego zginanie i może prowadzić do pęknięć. Zamiast tego stosuje się wzór siatki (hatch pattern), który redukuje sztywność, zachowując odpowiednią przewodność elektryczną. Wypełnienie miedzią zazwyczaj wynosi od 50% do 75%, co stanowi optymalny kompromis między elastycznością a funkcjonalnością.
Projektując warstwę mocy (PWR lub GND), należy również pamiętać o minimalizacji zakłóceń elektromagnetycznych (EMI) oraz obciążalności prądowej. Wzór siatki na warstwie mocy powinien być zaprojektowany tak, aby zachować odpowiednią przewodność, nawet przy dużych prądach, poprzez zwiększenie szerokości ścieżek i zmniejszenie odstępów między nimi.
Na etapie projektowania warto przeprowadzać symulacje mechaniczne i termiczne, aby sprawdzić, jak warstwa mocy zachowa się w przewidywanych warunkach pracy. Prototypy powinny być testowane w warunkach dynamicznych, aby zidentyfikować potencjalne słabe punkty konstrukcji i wprowadzić niezbędne poprawki.
Ostatecznie, projektowanie warstw mocy w obwodach flex wymaga kompromisu między wymogami mechanicznymi a elektrycznymi. Odpowiednie zastosowanie wzoru siatki, unikanie dużych obszarów miedzi w strefach gięcia oraz zapewnienie równowagi pomiędzy warstwami miedzi to podstawy, które pozwalają stworzyć niezawodny i trwały projekt dostosowany do specyficznych potrzeb aplikacji.
Kolejną kwestią jest ułożenie ścieżek w obwodach typu flex, które wymaga szczególnej uwagi ze względu na specyfikę pracy tych konstrukcji. Jednym z kluczowych elementów jest unikanie koncentracji ścieżek w jednej warstwie. Jak pokazuje rysunek poniżej, prowadzenie ścieżek wyłącznie w jednej warstwie powoduje nierównomierny rozkład naprężeń w strefach gięcia, co może prowadzić do uszkodzenia materiału lub pękania ścieżek. Zalecane jest równomierne rozmieszczenie ścieżek na różnych warstwach flexa, aby naprężenia były równomiernie rozkładane, co zwiększa trwałość całej konstrukcji.
Symetria w układzie ścieżek odgrywa tutaj kluczową rolę. W przypadku gęstego prowadzenia ścieżek na jednej stronie flexa, a ich niewielkiego zagęszczenia po drugiej stronie, dochodzi do nierównowagi mechanicznej, która może skutkować deformacjami podczas produkcji i użytkowania. Dlatego w projektach wielowarstwowych należy dążyć do równoważenia ilości miedzi na każdej warstwie. Dodatkowo w strefach gięcia ścieżki powinny być prowadzone równolegle do osi gięcia, co minimalizuje ryzyko ich uszkodzenia. Należy unikać prowadzenia ścieżek pod kątem lub na skos, ponieważ zwiększa to podatność na pęknięcia.
Uwzględnienie tych zasad w projektowaniu ścieżek w obwodach flex pozwala zminimalizować ryzyko uszkodzeń mechanicznych, poprawić niezawodność konstrukcji oraz wydłużyć żywotność urządzeń. Kluczowe jest przemyślane rozmieszczenie ścieżek, symetria układu oraz odpowiednie zaprojektowanie stref gięcia, które zapewniają trwałość obwodu nawet w najbardziej wymagających warunkach pracy.
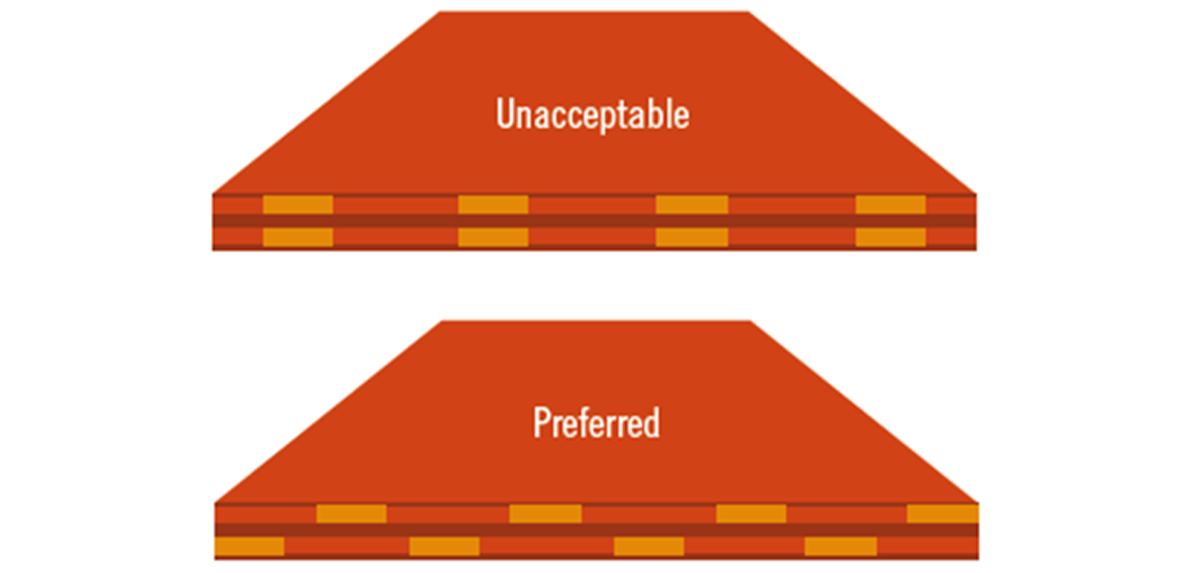
Symetria. Źródło rysunku: Proto Express
Ścieżki są stopniowo zwężane w strefie przejściowej, co zmniejsza koncentrację naprężeń. Płynne przejście kształtu ścieżek pozwala na bardziej równomierny rozkład obciążeń mechanicznych podczas zginania. Dzięki temu elastyczny obwód jest bardziej odporny na zmęczenie materiału, co znacznie zwiększa jego trwałość i niezawodność.
Wnioskiem z analizy rysunku jest to, że w projektowaniu obwodów flex należy unikać ostrych krawędzi i nagłych zmian szerokości ścieżek. Stopniowe zwężanie i zaokrąglone kształty w strefach przejściowych są kluczowe, aby zapewnić równomierne rozłożenie naprężeń. Taki sposób prowadzenia ścieżek nie tylko poprawia odporność mechaniczną obwodu, ale także zwiększa jego niezawodność w aplikacjach, gdzie flex jest narażony na dynamiczne lub powtarzające się zginanie.
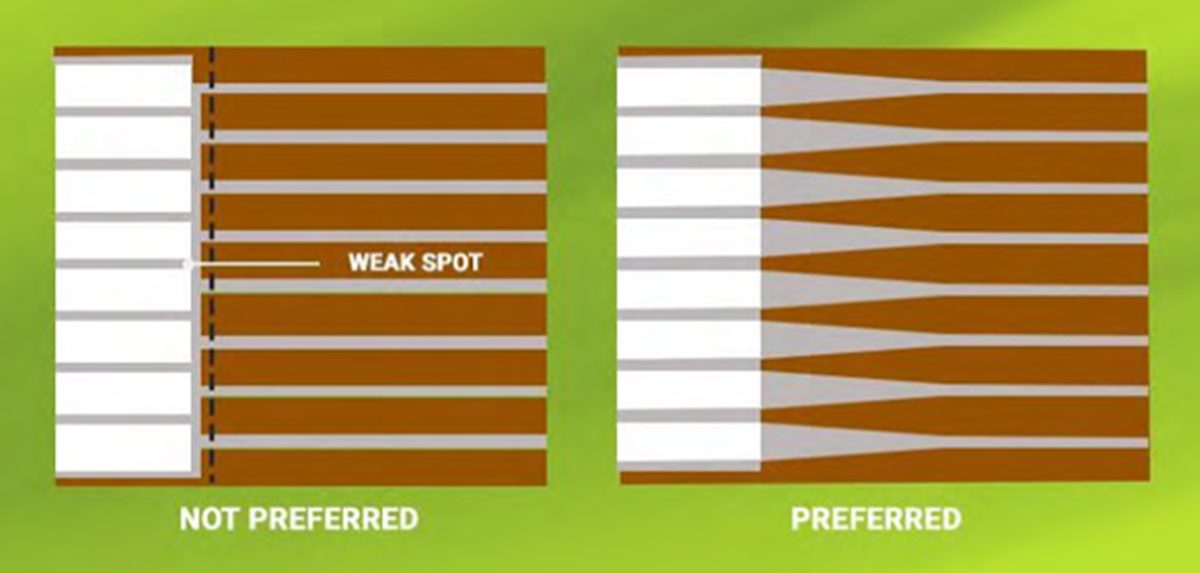
Strefy przejściowe. Źródło rysunku: Proto Express
Kolejnym ważnym zagadnieniem, między innymi w laminatach elastycznych, są Łezki (teardrops). Jest to technika stosowana w projektowaniu PCB, polegająca na rozszerzeniu obszaru połączenia ścieżki z padami lub przelotkami (via) w taki sposób, aby przybrał on kształt łzy. Rozwiązanie to ma kluczowe znaczenie w projektach wymagających wysokiej niezawodności oraz odporności na potencjalne problemy mechaniczne i elektryczne. Łezki wzmacniają połączenie ścieżki z padami lub przelotkami, zmniejszając ryzyko uszkodzenia mechanicznego podczas procesu produkcji, montażu lub użytkowania. W miejscach, gdzie ścieżka łączy się z padami lub via, dochodzi do koncentracji naprężeń mechanicznych, co może prowadzić do pęknięć miedzi. Dodanie łezki rozkłada te naprężenia na większą powierzchnię, zwiększając trwałość połączenia.
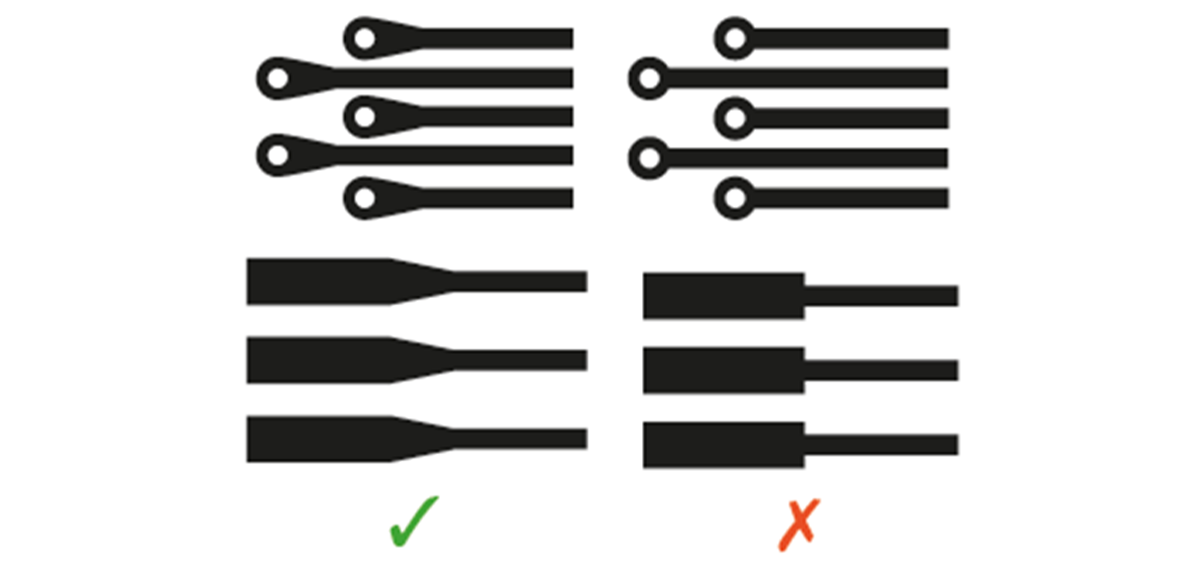
Łezki. Źródło rysunku: Proto Express
Ciekawą techniką, związaną z wzmocnieniem przelotek lub punktów lutowniczych w celu zwiększenie ich trwałości mechanicznej i odporności na uszkodzenia wynikające z naprężeń, jest użycie kotwic (anchor). Rozwiązanie to jest szczególnie istotne w aplikacjach, gdzie elastyczne obwody są narażone na częste zginanie, wibracje lub inne formy mechanicznego oddziaływania. Kluczowym elementem tej techniki jest zastosowanie dodatkowego „kotwienia”, które polega na rozgałęzieniach metalizowanej warstwy wokół przelotki lub punktu lutowniczego. Dzięki temu miedź jest lepiej zakotwiczona w materiale podłoża, takim jak poliamid, co zmniejsza ryzyko jej oderwania podczas zginania lub pracy w trudnych warunkach.
Warstwa ochronna, czyli coverlay, również odgrywa istotną rolę w tej technice. Otwór w warstwie coverlay zaprojektowany wokół przelotki pozwala na łatwy dostęp do punktu lutowniczego, jednocześnie zapewniając wsparcie i ochronę przylegających ścieżek.
Przedstawiona metoda stanowi przykład doskonale zaprojektowanego podejścia, które łączy optymalizację mechaniczną z funkcjonalnością, zapewniając długotrwałą wytrzymałość elastycznych PCB.
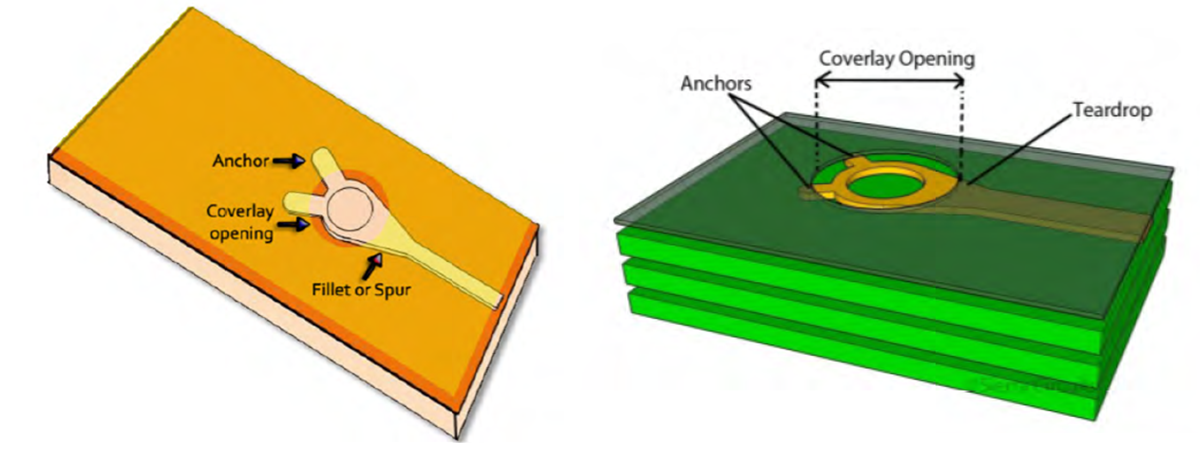
Kotwice. Źródlo rysunku Proto Express
Projektowanie elastycznych obwodów drukowanych (FPC) to fascynujące, ale również wymagające zadanie, które wymaga szczególnej uwagi na aspekty mechaniczne, elektryczne i środowiskowe. Zrozumienie specyficznych wymagań takich układów, w tym odpowiedniego promienia gięcia, doboru materiałów oraz zarządzania integralnością sygnału, jest kluczem do stworzenia niezawodnych i efektywnych rozwiązań.
Stosowanie najlepszych praktyk projektowych, takich jak unikanie ostrych kątów ścieżek, właściwe rozmieszczenie warstw, wprowadzanie łezek (teardrops) w newralgicznych punktach połączeń znacząco zwiększa trwałość i niezawodność elastycznych PCB.
Źródło zdjęć Flex PCB i Rigit Flex PCB na zdjęciu tytułowym: Semicon sp. z o.o.