Fotolitografia nie zawsze „foto” – Grzegorz Kamiński opisuje procesy nanoszenia wzorów na płytki półprzewodnikowe
W poprzedniej publikacji starałem się pokazać, że nie tylko postęp w procesie naświetlania przyczynia się do postępu technologii półprzewodnikowych. Oczywiście, ze względu na charakter tekstu, ograniczyłem się tylko do kluczowych osiągnięć w zakresie jednego z procesów – fotolitografii. Przeglądając sukcesy w tym zakresie, znalazłem informację o nowej maszynie do transferu wzoru maski na płytkę półprzewodnikową. Wielokrotnie pojawiają się informacje o tym, co udało się wdrożyć firmie ASML, a ta wiadomoć pojawiła się i zniknęła, praktycznie bez komentarzy. Zastosowana w tej maszynie technologia już nie jest foto, a ponadto w pewien sposób wróciła do początków technologii przenoszenia wzoru z maski na płytkę półprzewodnikową.
W tym artykule porównam dostępne obecnie systemy do litografii. W komentarzach do poprzedniego testu otrzymałem cenne uwagi, że nie opisałem całego proces fotolitografii, a poprawniej litografii. Zgadzając się z tym, przedstawię tutaj skrótowo cały proces. Skłoniły mnie do tego również artykuły w stylu „Układ scalony w 10-ciu krokach”, sugerujące że gotowy układ scalony można wykonać stosunkowo szybko. Takie publikacje trochę mnie irytują, ponieważ w okresie braków w dostępności podzespołów półprzewodnikowych, gdy jeszcze pracowałem w dziale sprzedaży firmy onsemi, wielokrotnie musiałem tłumaczyć, dlaczego np. w 2-3 tygodnie nie możemy dostarczyć podzespołów.
Wiele z tekstów, w tym te o firmie ASML sugerują, że taki proces litografii robimy tylko jeden raz i już wszystko jest gotowe. Wręcz przeciwnie – by wytworzyć półprzewodnikowy monolityczny układ scalony, musimy wykonać setki procesów technologicznych, w tym wielokrotnie proces fotolitografii, który nie zawsze jest „foto”. A to wymaga czasu, bo procesów fizyko-chemicznych nie da się przecież skrócić.
Proces fotolitografii
Rysunek poniżej przedstawia „wzorcowy” proces fotolitografii.
Wafer – płytka półprzewodnikowa, załóżmy że krzemowa, która będzie podlegać kolejnym procesom. Dalej już będę używał określenia „płytka krzemowa”, chociaż może być także zwrot „płytka półprzewodnikowa”.
Photoresist – substancja światłoczuła, dzięki której wzór z maski możemy przenieść na płytkę krzemową.
Mask – czyli maska, na której znajduje się wzór do przeniesienia na płytkę krzemową.
10 etapów procesu
- Vapor Prime and Bake: Wilgoć z atmosfery jest dość szybko absorbowana na powierzchni płytek krzemowych. Powoduje to, że fotorezyst może nie mieć odpowiedniej przyczepności do podłoża krzemowego, a to może powodować błędy w przenoszonym wzorze z maski na płytkę krzemową. W celu poprawy przyczepności fotorezystu do płytki krzemowej, a jednocześnie zatrzymania procesu absorbowania wilgoci przez wspomnianą płytkę, nanosi się na nią tak zwany primer. To taka angielska nazwa, oznaczająca substancję zwiększającą przyczepność. Jest kilka metod nanoszenia, ale to teraz pominę, bo ten tekst nie jest podręcznikiem technologii półprzewodnikowej. Przed nałożeniem primer’a płytka krzemowa jest podgrzewana w celu usunięcia nadmiaru wilgoci. Najczęściej jako primer stosuje się substancję, która w skrócie nazywa się HMDS. Pełna nazwa to heksametylodisilazan. Prawda, że fajna? Mnie się bardzo podoba.
- Coating: Nakładanie fotorezystu. Proces ten wykonywany jest najczęściej na wirówkach, gdzie kropla fotorezystu trafia na środek płytki krzemowej, a wirowanie i siła odśrodkowa rozprowadza ją na całą płytkę. Często ten proces można zobaczyć na filmach o wytwarzaniu podzespołów półprzewodnikowych. Wygląda bardzo efektownie.
- Soft Bake: Po nałożeniu fotorezystu płytka krzemowa jest podgrzewana do 60°C – 125°C. Ma to na celu odparowanie lotnych substancji, po czym fotorezyst staje się bardziej warstwą „lakieru” na powierzchni płytki krzemowej, a nie ciekłą substancją. Poprawia to również przyczepność fotorezystu do płytki. Metod podgrzewania jest wiele.
- Wafer Alignment and Exposure: To proces wykonywany m.in. na maszynach ASML. Poprzez maskę fotorezyst jest naświetlany światłem UV. Pod jego wpływem substancja światłoczuła zmienia swoje właściwości. W kolejnych procesach będziemy mogli usunąć naświetlony fotorezyst – dla fotorezystów pozytywowych lub nienaświetlony fotorezyst – w przypadku, gdy zastosowaliśmy fotorezyst negatywowy. To co opisałem, wyczerpuje znaczenie słowa „Exposure” w tytule tego procesu. Ale co z „Alignment”? Cały proces fotolitografii trzeba powtarzać wielokrotnie, by uzyskać gotowy układ scalony. Poszczególne warstwy muszą być położone dokładnie w określonym miejscu i dlatego przenosząc wzór kolejnej warstwy z maski na płytkę krzemową musimy ją zgrać („Alignment”) z wcześniej wytworzonymi. Ten proces będzie jeszcze dokładniej opisany w dalszej części artykułu.
- Develop: Przy pomocy odpowiednich substancji chemicznych, zwanych wywoływaczami – tak jak w procesach fotograficznych – usuwany jest fotorezyst, naświetlony dla fotorezystów pozytywowych lub nienaświetlony fotorezystu negatywoego. W ten sposób odzwierciedlany jest wzór na masce.
- After Develop Inspection: Musimy być pewni, że wywoływacz usunął fotorezyst z obszarów, gdzie powinien być usunięty i pozostawił tam, gdzie miał pozostać. Na tym etapie mamy jeszcze szansę, by „powtórzyć” wywołanie i poprawić błędy.
- Hard Bake: Ponownie podgrzewamy płytkę krzemową pokrytą już wywołanym fotorezystem do temperatury w zakresie 120-150°C. Po tym procesie już nie będziemy mogli usunąć pozostałości fotorezystu z niepożądanych miejsc. Można to porównać do utwardzenia „lakieru”. Fotorezyst zyskuje także odporność na kolejne procesy fizyko-chemiczne. Musi dać nam gwarancję, że w kolejnych etapach usuniemy warstwę np. tlenku krzemu SiO2 z tego miejsca, z którego chcemy, a fotorezyst będzie barierą dla wytrawiacza SiO2.
- Etch: Trawienie może być mokre lub suche (Wet or Dry). Najprościej mówiąc, trawienie mokre to proces czysto chemiczny, gdzie stosujemy odpowiednie wytrawiacze w zależności od rodzaju warstwy. Trawienie suche to proces fizyko-chemiczny, w którym najczęściej mieszanina gazów trawia właściwą warstwę. Zaletą tego procesu jest jego izotropowość, czyli trawienie ukierunkowane. Trawienie mokre jest generalnie anizotropowe, czyli wytrawiacz usuwa materriał w głąb i „na boki”, co oczywiście ma wpływ na możliwości precyzyjnego przenoszenia wzoru z maski na obrabianą w tym procesie warstwę. Ten proces ma na celu przeniesienie wzoru z maski już na właściwą warstwę na płytce krzemowej. Jest to bardzo interesujący proces technologiczny i warto byłoby go oddzielnie opisać, ale w tym tekście na tym poprzestańmy.
- Ion implant: To modyfikacja procesu, gdzie fotorezyst stanowi barierę dla jonów domieszki wprowadzanych do płytki krzemowej w procesie implantacji. Na temat metod domieszkowania i po co się to robi napiszę oddzielny artykuł.
- After Etch Inspection: Musimy sprawdzić czy wykonaliśmy proces trawienia poprawnie. W tym momencie możemy jeszcze skorygować ewentualne błędy procesu.
- Photoresist strip and wafer clean: Na koniec procesu fotolitografii musimy usunąć fotorezyst. Używane są do tego substancje, które potocznie określa się mianem „stripper”. Po polsku możemy chyba użyć słowa „zmywacz”, bo już kilka razy porównałem fotorezyst do lakieru. Ta substancja musi mieć także szereg określonych właściwości, np. nie może uszkadzać warstwy na której znajduje się fotorezyst oraz warstw odsłoniętych, pozbawionych fotorezystu po procesie trawienia. Proces mycia płytek krzemowych (wafer clean) także zasługuje na osobny artykuł.
Nazywając poszczególne etapy procesu fotolitografii użyłem nazw angielskich, ale w opisach zastosowałem ich polskie odpowiedniki opisałem je dokładnie z uwagi na brak właściwego słowa w rodzimym języku. Istnieją pewne modyfikacje tego procesu np. technika lift-off. Muszę jednak upraszczać, zarówno ze względu na objętość tekstu, jak i w celu lepszego zrozumienia przez szerokie grono czytelników tego portalu.
Jak to przedstawiłem powyżej, tylko sam proces fotolitografii ma dziesięć podstawowych kroków. Nie da się zatem w dziesięciu krokach zrobić półprzewodnikowego układu scalonego. Ogólny schemat procesu wytwarzania chipu układu scalonego, jak już kiedyś wspomniałem, jest taki jak na poniższym rysunku:
Po fotolitografii konieczne jest mycie płytek. Nie jest to jednak istotne dla zrozumienia procesu wytwarzania podzespołów półprzewodnikowych. Ważne jest tylko to, że zarówno proces fotolitografii jak i mycia płytek powtarza się wielokrotnie. Pomiędzy nimi wykonuje się szereg innych procesów technologicznych. Ile jest tych etapów?
Według moich danych oraz informacji firmy TSMC, dla technologii CMOS 350-110 nm wymaganych jest ok. 20 procesów fotolitografii. W technologiach z tego zakresu wykonuje się układy analogowe BiCMOS, gdzie w jednym układzie scalonym są układy bipolarne i CMOS. W takim przypadku liczba fotolitografii może wynieść nawet 30. Ilość fotolitografii dla najbardziej zaawansowanych technologii 5-7 nm może sięgać 80. Oznacza to, że produkcja układu scalonego może liczyć 1000 kroków, a jest to tylko etap wytworzenia chipu. Zostaje nam jeszcze montaż w obudowę. Wszystkie te procesy są bardzo precyzyjne, mają charakter fizyko-chemiczny, a sukces jest zdeterminowany powtarzalnością całego procesu. Dlatego wytworzenie chipu układu scalonego trawa wiele miesięcy. Warto o tym pamiętać, gdy czytamy tekst w rodzaju „Układ scalony w 10-ciu krokach”!
Skupmy się na naświetlaniu
Największe emocje – biorąc pod uwagę liczbę publikacji – wzbudzają maszyny do procesu EUV, produkowane przez ASML, czyli de facto do naświetlania fotorezystu (ang. exposure). Dlatego postaram się ten proces przedstawić nieco bliżej, tym bardziej, że w poprzedniej publikacji była już o tym mowa. Można to potraktować jako uzupełnienie poprzedniego tekstu.
W tabeli poniżej zebrałem dane wszystkich maszyn do naświetlania, możliwych do wykorzystania w procesach technologii sub-mikrometrowych:
Niektórych danych brak, bo nie zostały opublikowane przez producentów. W wielu wypadkach można się ich domyślić, ale nie uzupełniałem tabeli na podstawie domysłów. Współczynnik k1 został wyliczony na podstawie dostępnych informacji. Teoretyczna minimalna wartość tego współczynnika wynosi 0,25. Związany jest on z trudnością procesu litografii. Każda generacja układów scalonych opiera się na mniejszych rozmiarach geometrycznych, określanych jako node lub technologia np. technologia 5 nm. Wymaga to lepszej rozdzielczości technik litografii optycznej, używanych do ich wytwarzania. Litografię optyczną nazywamy fotolitografią. Minimalny rozmiar, jaki możemy osiągnąć w tym procesie wynosi w przybliżeniu:
W tabeli wartość tego minimalnego rozmiaru CD określona jest jako rozdzielczość.
λ – długość fali UV światła stosowanego do naświetlania; NA – apertura numeryczna
Dodatkowy komentarz na temat współczynnika k1: Napisałem, że jego teoretyczna minimalna wartość wynosi 0,25. W tabeli powyżej najmniejsza wyliczona wartość k1, według danych od producentów stepperów, wynosi 0,266. Najlepsza rozdzielczość CD to 8 nm, przy k1 = 0,326. No to jakim cudem możemy wytwarzać chipy z rozdzielczościami CD = 3-7 nm? Mamy kilka dodatkowych technik, o których pisałem w poprzednim tekście, a są to wstępne zniekształcanie obrazu (ang. optical proximity correction, OPC) oraz double-patterning (DP). Firma Mentor Graphics, obecnie Siemens dokonała obliczenia skorygowanego k1, dla danej technologii.
Rysunek należy rozumieć tak, że razem z DP stosowane jest także OPC, tylko zaznaczono na nim, która technika ma decydujący wpływ na uzyskane k1.
W tabeli jest jeszcze kolejne pojęcie do wyjaśnia, a mianowicie overlay. Nie do końca wiedziałem, jak je poprawnie przetłumaczyć. Można go określić jako dokładność centrowania/pozycjonowania. Jak już wspomniałem, proces fotolitografii jest powtarzany wielokrotnie. Wzór przeniesiony na płytkę musi być odpowiednio pozycjonowany względem kolejnego wzoru, który zamierzamy przenieść. Dokładność tej operacji określana jest jako overlay. Jak widać w tabeli, overlay jest mniejsze od CD.
Obraz z maski jest rzutowany jest na płytkę, dlatego ten proces nazywany jest fotolitografią projekcyjną. Współczynnik redukcji podany w tabeli określa, ile razy obraz z maski jest zmniejszany względem tego przenoszonego na płytkę. Gdy wynosi 4:1 oznacza to, że obraz na masce jest 4 razy większy od tego na płytce krzemowej. Wszystkie maszyny z tabeli to tak zwane steppery, dlatego określane jest także pole naświetlenia. W jednym procesie naświetlany jest tylko obszar podany w kolumnie jako pole naświetlania, po czym stolik z płytką się przesuwa i naświetlany jest kolejny obszar płytki krzemowej. Dlatego ten proces często nosi nazwę step-and-repeat i z tego powodu maszyny zwane są stepperami. Przykładowo dla płytki o średnicy 300 mm (12”), musimy wykonać >80 kroków/naświetlań (step-and-repeat). Łatwo policzyć że jeden „błysk” musi być w zakresie dziesiątych części sekundy, aby uzyskać wydajności podane w tabeli.
Jeden z producentów podaje minimalną i maksymalną aperturę numeryczną. Dlaczego? Ten parametr w optyce urządzenia można regulować, bo jest jeszcze jeden istotny parametr procesu naświetlania – głębia ostrości. Stosowany jest w optyce do określania zakresu odległości, w którym obiekty obserwowane przez urządzenie optyczne sprawiają wrażenie ostrych (czyli mają wyraźne kontury). Głębię ostrości DOF (and. depth of focus) w przybliżeniu określa wzór:
λ – długość fali UV światła stosowanego do naświetlania; NA – apertura numeryczna; k2 – ma podobne znaczenia jak k1. Nie mogłem go policzyć, bo żaden z producentów nie podał DOF. Teoretycznie k2 wynosi ok. 0.5.
Poprawa DOF wiąże się z pogorszeniem rozdzielczości CD. Obraz musimy być ostry, ponieważ w przeciwnym razie proces naświetlania nie zdefiniowałby dokładnie kształtów na płytce krzemowej. Dla pierwszej litografii oraz dla definiowania rozdzielczości maszyny DOF nie jest istotne. Jednak w kolejnych procesach płytka krzemowa ma już nałożone następne warstwy np. utleniania czy CVD i nie jest idealnie płaska. Wytrawiany selektywnie np. dwutlenek krzemu SiO2 powoduje, że są nia niej „góry i doliny” i to o wysokościach zbliżonych do CD. Jak widać, przeniesienie obrazu odpowiedniej jakości z maski na płytkę krzemową nie jest proste.
W tabeli jest także podane źródło światła. Zakres źródeł światła stosowanych dla fotolitografii przedstawia rysunek poniżej:

Zakres stosowanych źródeł światła w fotolitografii. Źródło: Jerzy Rużyłło – Guide to Semiconductor Engineering (World Scientific 2020)
Zaznaczone strzałkami długości fali to tzw. g-line 436 nm i i-line 365 mm lampy rtęciowej. 248 nm to długość fali lasera KRF, a 193 nm to długość fali światła lasera ArF. Osobnego i dłuższego opisu wymaga źródło światła dla EUV – 13.5 nm. Te wszystkie długości światła są stosowane w stepperach. Ale jakie metody naświetlania były przed erą stepperów?
Pierwszy (a) to tzw. contact printing – naświetlanie kontaktowe. Maska styka się dość mocno z płytką krzemową. Oczywiście pomiędzy maską a płytką jest naświetlany fotorezyst. Rysunek poniżej dobrze to przedstawia. Tej techniki zaniechano, ponieważ łatwo było o uszkodzenia maski, co prowadziło do sytuacji, że defekt przenosił się na kolejne płytki krzemowe. Często też trzeba było wymieniać maski. Z tego powodu spadał tzw. uzysk, czyli liczba dobrych chipów do wszystkich chipów na płytce. Część wytwarzanych chipów była uszkodzona.
Kolejną metodą był proximity printing (b), czyli naświetlanie zbliżeniowe. Trzeba było zmodyfikować optykę, by zredukować tak zwane podświetlenia. Maska znajdowała się o kilka mikrometrów od warstwy fotorezystu. Dzięki temu „żywotność” masek wzrosła, podobnie jak uzysk. Dzięki temu koszty produkcji spadły. W obu tych metodach naświetlano jeden raz całą płytkę. Jednakże proces ten pozwalał osiągnąć rozdzielczość na poziomie 2 μm. Potrzebowaliśmy lepszych rozdzielczości, a to nam dało projection printing ( c ) – naświetlanie projekcyjne. Było wiele systemów tego naświetlania, także ze współczynnikiem redukcji 1:1, a nawet 10:1.
Obecne są te zawarte w tabeli. Umożliwiają uzyskanie rozdzielczości praktycznej od 2 nm do 1 μm.
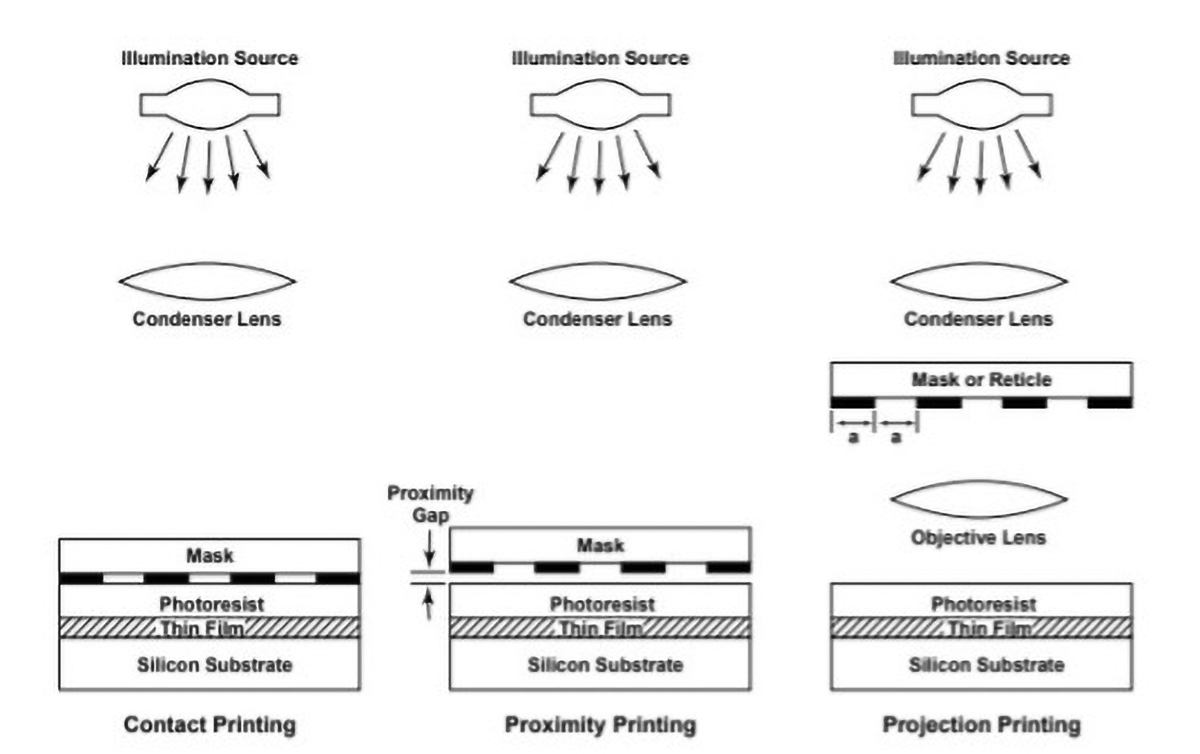
Rodzaje naświetlania w fotolitografii. Źródło: Jerzy Rużyłło – Guide to Semiconductor Engineering (World Scientific 2020) oraz ICE Corp.
Naświetlanie projekcyjne jest obecnie najpowszechniej stosowaną metodą. Nie napisałem czy dalej stosuje się naświetlanie zbliżeniowe – proximity printing. Jestem pewien, że tak. To bardzo tania metoda, maszyny do naświetlania są niedrogie, szczególnie jak porównamy je z urządzeniami projekcyjnymi, nawet do fotolitografii DUV. Maszyna do DUV kosztuje kilkadziesiąt milionów dolarów, nie wspominając już o maszynach, gdzie źródło światła jest w zakresie EUV. Proste diody i tranzystory można wykonywać z użyciem naświetlania zbliżeniowego. Nawet w bardzo skomplikowanych układach scalonych ostatnia fotolitografia zazwyczaj nie wymaga fotolitografii DUV, a zwykłe naświetlanie zbliżeniowe jest wystarczające. Zerknijmy na zdjęcie poniżej.
Dookoła chipu widać pola, do których są podłączone wyprowadzenia drutowe łączące chip z jego obudową (czarne kropki z „ogonkiem”). Wielkość pola metalizacji do podłączenia takiego wyprowadzenia wynosi ok. 100 μm. Jednym z ostatnich procesów w wytwarzaniu chipu jest pokrycie jego warstwą zabezpieczającą, najczęściej jest to dwutlenek krzemu SiO2 lub azotek krzemu Si3N4. Później w tej warstwie musimy wykonać otwory do metalizacji w miejscach, gdzie będą podłączenia drutowe. Ponieważ otwory będą mieć bok o wymiarze ok. 100 μm, to do takiego procesu fotolitografia zbliżeniowa jest jak najbardziej wystarczająca. Z tego powodu sądzę, że ten rodzaj naświetlania jest ciągle w użyciu.
Jeszcze raz podkreślę: sama maszyna do naświetlania, nawet najwspanialsza to nie wszystko, by osiągnąć wspomniane rozdzielczości na poziomie 3 nm.
Uwaga końcowa do tej części: W zakresie EUV ASML nie ma obecnie żadnego konkurenta. Ale już w zakresie DUV są 3 firmy, które ze sobą rywalizują na rynku światowym. Steppery wytwarza także firma chińska, ale jest ona obecna tylko na wewnętrznym rynku i trudno uzyskać wiarygodne dane co do jakości tych maszyn. Mnie zainteresowało nowe rozwiązanie firmy Canon, mogące konkurować z rozwiązaniem EUV ASML-a.
EUV z ASML
Powstało wiele tekstów na temat tego, jak działa urządzenie do naświetlania firmy ASML pracujące w EUV (Extreme UV). Schemat poglądowy tego urządzenia przedstawia rysunek poniżej:
Jak widać, zamiast klasycznej optyki z soczewkami mamy tylko zwierciadła. Niestety na zakres światła UV 13,5 nm, które jest już bliskie zakresowi tzw. soft-X-ray, nie potrafimy wytworzyć soczewek. To była ogromna zmiana, bo do tego typu urządzenia trzeba było wytworzyć odbiciową maskę (Reflective Mask). Jak widzieliśmy wcześniej na schematach, klasyczna maska jest stosunkowo prosta, jeśli chodzi o zasadę działania. Są obszary, gdzie światło przechodzi i wtedy fotorezyst jest naświetlany, są też obszary, gdzie światło jest blokowane.
W wypadku EUV mamy strefy maski gdzie światło się odbija i strefy, gdzie światło musi zostać zaabsorbowane przez materiał maski. Możliwe, że światło w tych miejscach odbija się pod takim kątem, że nie trafia na płytkę i rozprowadzony na niej fotorezyst. Nie wiem jak to jest faktycznie. To temat do weryfikacji. Chciałbym tu podkreślić, że temat masek kompletnie pominąłem w tym tekście, bo jest obszerny sam w sobie. Wszystko inne przebiega klasycznie, czyli jest to stepper o współczynniku redukcji 4:1 i polu naświetlania 26×33 mm, tak jak w wielu innych stepperach.
Ponieważ inny jest układ optyczny, to oczywiste jest, że apertura numeryczna też jest inna. Podobnie ja długość fali światła: 13,5 nm. W większości publikacji ten fakt nie jest komentowany. Jest światło o długości fali 13,5 nm i tyle. Dla DUV jest to dosyć proste – laser np. ArF świeci z długością fali 193 nm. Ale co świeci z długością fali 13,5 nm? Nie mamy takiego lasera. Nie ma też żadnego naturalnego źródła ekstremalnego światła ultrafioletowego (światło EUV). Jak zatem to jest ono wytwarzane? W pierwszym kroku otrzymujemy kroplę cyny, 50 tysięcy kropel na sekundę. Już to jest niezwykle trudne. W taką kroplę cyny „strzelamy” laserem gazowym CO2, o mocy ok. 2 kW. Kropla cyny jest podgrzewana, na chwilę trwającą nanosekundy, do niezwykle wysokiej temperatury, ok. 400 000 stopni Celsjusza, wówczas atomy rozpadają się na wolne elektrony i dodatnio naładowane jony o różnych ładunkach.
Takie rozbite atomy tworzą plazmę, czyli czwarty stopień skupienia materii. Wiele z tych jonów jest w stanie wzbudzonym: jeden lub więcej orbitujących elektronów ma dodatkową porcję energii. Elektrony te krążą po orbicie znajdującej się dalej od jądra atomowego niż najbliższa orbita. Kiedy wracają na orbitę bliższą jądra, dodatkowa energia jest uwalniana w postaci promieniowania EUV o długości fali 13,5 nm. Trzeba podkreślić, że możliwych przejść pomiędzy orbitami jest ponad 10 miliardów. Naukowcy musieli więc wiedzieć, jak taki proces zasymulować, by mieć pewność, że to promieniowanie świetlne w zakresie UV daje głównie światło o długości fali 13,5 nm, a nie również inne długości fali. Wykorzystali do tego superkomputer w Laboratorium Narodowym w Los Alamos, USA. Tak, jest to dokładnie to samo miejsce, gdzie została opracowana w latach 40 XX wieku bomba atomowa. Wynik symulacji przedstawia rysunek poniżej:
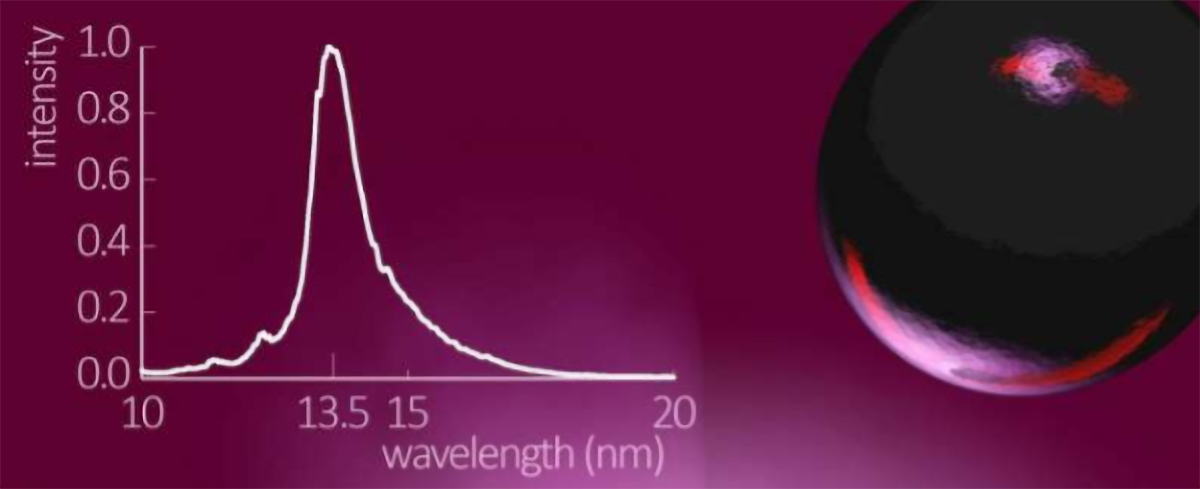
Rozkład promieniowania plazmy cyny. Źródło grafiki pod linkiem
Laser gazowy CO2 działa w zakresie dalekiej podczerwieni, długość fali światła emitowanego przez ten laser wynosi 10 μm. Wadą jego jest sprawność, więc aby uzyskać moc lasera ok. 2 kW, potrzeba zasilacza o mocy 20kW. Trochę słabo, jeśli mamy mieć w fabryce kilka lub kilkanaście takich maszyn działających praktycznie nieprzerwanie. Dlatego obecnie naukowcy testują laser neodymowy na YAG (Nd:YAG), pracujący w bliskiej podczerwieni. Długość fali światła takiego lasera wynosi 1064 nm. Dość powszechnie stosuje się je w medycynie i kosmetologii np. do usuwania tatuaży.
Taki laser nie wymaga aż tak dużych mocy zasilacza, by uzyskać równie dobre wyniki. Pierwsze testy wykazały, że rozkład promieniowania plazmy cyny jest nawet lepszy dla lasera Nd:YAG. Pewnie kolejna generacja urządzeń firmy ASML będzie wyposażona już w taki laser do generowania światła 13,5 nm. Dla odbiorców ważne są nie tylko parametry i cena, ale również tzw. TCO, czyli ang. total cost of ownership (całkowity koszt posiadania), uwzględniający koszty eksploatacji. Taka maszyna w fabryce przyrządów półprzewodnikowych będzie pracować przez kilkanaście lat, a może nawet więcej. Więcej na temat generacji światła 13,5nm tutaj.
Na koniec Nanoimprint Stepper firmy Canon
No i doszliśmy do tytułowego tematu czyli fotolitografii która nie jest foto. Jest wiele takich technologii: elektronolitografia, x-ray litografia, bezpośrednie naświetlanie laserem UV (direct write laser lithography). Jednak wszystkie te technologie nie są powszechnie stosowane w przemyśle półprzewodnikowym przy produkcji układów scalonych. Są natomiast używane do wytwarzania specjalnych przyrządów półprzewodnikowych lub przy badaniach naukowych z tej dziedziny. Wszystkie one mają swoje niewątpliwe zalety. Wadą jest mała wydajność, a tym samym duży koszt produkcji. Dlatego, jak już wspomniałem, używa się ich w aplikacjach specjalnych i małoseryjnych.
Inna sprawa to nowa maszyna firmy Canon, typ FPA1200NZ2C. Ma wydajność 80 płytek na godzinę i zapewnia rozdzielczość 15 nm, porównywalną z poprzednią generacją maszyn EUV firmy ASML. Producent twierdzi nawet, że po dopracowaniu technologii da się osiągnąć rozdzielczość 10 nm przy dokładności pozycjonowania (overlay) 1 nm. To bardzo obiecujące rezultaty. Informacja o tej technologii pojawiła się i zniknęła praktycznie bez komentarzy. Co jest bardzo interesujące, maszyna ta jest stosowana przez firmę KIOXIA w jej fabryce Yokkaichi, przy produkcji pamięci Flash NAND właśnie w technologii 15 nm.
To bardzo interesujące, bo świadczy o tym, że jest to produkt, który znalazł rzeczywiste zastosowanie i nie jest tylko informacją promocyjną czy końcowym etapem opracowania produktu. Wszystkie informacje o tej technologii uzyskałem ze strony Canon.
Litografia nanoimprint (NIL) to nie jest nowa metoda. Była stosowana w optyce, fotonice czy biotechnologii. W produkcji przyrządów półprzewodnikowych jako pierwsza użyła jej firma Toshiba dla technologii 22-30 nm. KIOXIA, która powstała z działu Toshiby produkującego pamięci, jest naturalnym kontynuatorem tego projektu. To metoda wytwarzania wzorów w skali nanometrowej. Jest to prosty proces o stosunkowo niskich kosztach, dobrej wydajności i wysokiej rozdzielczości. Wzór z maski tworzy wzory poprzez mechaniczną deformację rezystu i późniejsze procesy. Rezyst zwykle jest monomerem lub polimerem, który jest utwardzany ciepłem lub światłem UV podczas odciskania przy pomocy maski. Przyczepność między rezystem a maską jest krytyczna dla tego procesu i musi być dokładnie kontrolowana, aby umożliwić prawidłowe uwalnianie/podniesienie maski. Poniższy rysunek pochodzi ze strony firmy Canon i ilustruje różnice pomiędzy klasyczną fotolitografią a procesem NIL:
Ponieważ w produkcji pamięci Flash NAND liczba warstw przekracza nawet 200, to krytycznym procesem jest centrowanie/pozycjonowanie płytki krzemowej względem maski. Canon opracował proces zwany TTM, pozwalający w czasie rzeczywistym mierzyć dokładność pozycjonowania (overlay).
Oprócz technologii umożliwiającej pomiar informacji o odchyleniu położenia płytki względem maski, ważna jest również technologia dopasowania płytki i maski umożliwiająca precyzyjne pozycjonowanie z wzorami niższych warstw. Firma Canon opracowała opatentowany system, w którym lokalnie laser nagrzewa płytkę w celu jej termicznego odkształcenia. Powszechnie uważa się, że takie odkształcenie tylko pogarsza precyzję pozycjonowania, ale opatentowane rozwiązanie Canon z tym sobie radzi. Cały proces jest świetnie opisany w zamieszczonym krótkim, 3,5 min filmie na stronie której link podałem powyżej. Poniżej dwa zdjęcia z tego filmu:
Jak widać, wzór maski jest po prostu odciskany w warstwie rezystu. Kolejny krok to naświetlenie rezystu światłem UV w celu jego utwardzenia i ułatwienia procesu oddzielenia maski. Co się dzieje, gdy powstaną błędy w procesie rozdzielenia rezystu i maski, przedstawia kolejny kadr z filmu. To jeden z krytycznych etapów procesu:
Jak podaje Canon, wydajność procesu to 80 płytek na godzinę. To jest dwa razy mniej niż w systemach EUV firmy ASML. Jednakże wydaje się, że urządzenie Canon może być mniej kosztowne, zużywające mniej energii elektrycznej a co za tym idzie – TCO czyli ang. total cost of ownership ( całkowity koszt posiadania) powinien być niższy niż w przyp[adku maszyny EUV z ASML.
Zobaczymy jak w przyszłości rozwiną się obie technologie. Dzisiaj górą jest ASML, bo umożliwia już teraz produkcję w technologiach o rozdzielczości na poziomie 2-3 nm. Być może obie technologie się rozwiną i znajdą zastosowania, w zależności od zapotrzebowania na określone przyrządy półprzewodnikowe. Technologia firmy Canon wygląda bardzo obiecująco i jest litografią, a nie fotolitografią. Co ciekawe, trochę wróciliśmy do korzeni, bo znowu maska jest dociskana do rezystu, tak jak to było w porzuconej już w masowej produkcji metodzie „contact printing”.