[RAQ] Nowoczesne układy zasilania dla inteligentnych czujników
Pytanie:
Czy w nowoczesnych inteligentnych czujnikach można korzystać z tradycyjnych układów zasilania dla sensorów przemysłowych?
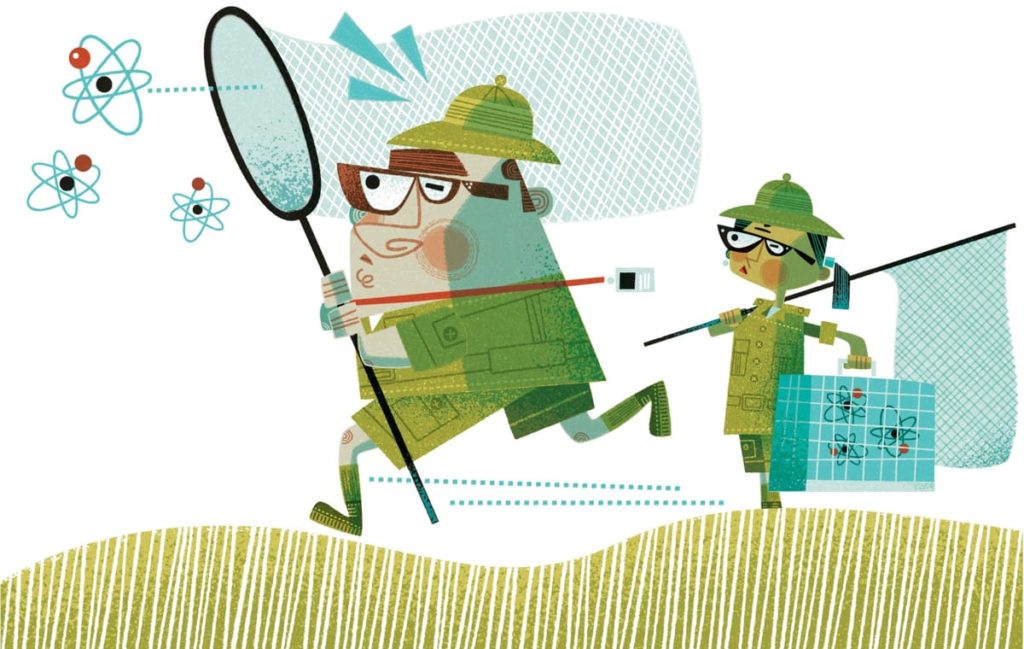
Odpowiedź:
Czasami tak, ale w większości przypadków niestety nie. Inteligentne sensory mają pewne specyficzne wymagania, które trzeba uwzględnić na etapie projektowania zasilacza.
Streszczenie
W artykule przedstawiono inteligentne sensory oraz wyzwania związane z projektowaniem dla nich układów zasilania. Omówimy także niektóre z dostępnych obecnie rozwiązań.
Wstęp
Obszar czujników przemysłowych jest obecnie pełen innowacji i wyzwań. Nowe wymagania obejmują m.in. zasilacze układów. Można wyróżnić kilka typowych przypadków, które trzeba uwzględnić. Często czujniki inteligentne trzeba zasilać z pojedynczej skrętki, przez którą również przesyłane są dane. Jest to możliwe dzięki technologii Single‑pair Power-over-Ethernet (SPoE).
Innym typowym przypadkiem są czujniki pobierające małą moc, zwykle pracujące na baterii. Warto wtedy zastosować układ zasilający o niskim prądzie spoczynkowym i bardzo wysokiej sprawności dla małej mocy.
Niektóre inteligentne czujniki wymagają zasilacza o bardzo niskim poziomie szumów. Przy pomiarze małych sygnałów jest to niezwykle ważne i pozwala zapewnić dokładność układu.
Zależy nam także na miniaturyzacji sensorów. Szukamy więc układów, które są małe i wielofunkcyjne. W artykule zaprezentujemy przykład układu SIMO (Single-Inductor Multiple-Output), który zawiera tylko jedną cewkę, a potrafi generować kilka napięć zasilających.
Czym są inteligentne czujniki przemysłowe?
Inteligentne czujniki przemysłowe, to urządzenia, które mierzą i wstępnie przetwarzają dane z otoczenia. Jest to dość nowoczesne podejście w porównaniu do tradycyjnego, gdzie czujnik miał za zadanie tylko pobrać dane i przesłać je do jednostki centralnej. Do przetwarzania danych w sensorach potrzebny jest oczywiście wbudowany mikrokontroler lub mikroprocesor. Wstępne przetwarzanie zmniejsza ilość danych wysyłanych do serwera, a to z kolei pozwala uprościć protokoły komunikacyjne.
Prostym przykładem takiej aplikacji jest sensor optyczny służący do wykrywania określonych informacji, takich jak obecność osoby, która przypadkowo wejdzie do obszaru produkcyjnego, narażając się na niebezpieczeństwo. Obraz musi być przetwarzany w taki sposób, aby można było jednoznacznie zidentyfikować obecność człowieka. Pozwoli to w razie potrzeby szybko wyłączyć maszyny i zapobiec wypadkom. Przydatne w takiej aplikacji jest właśnie przetwarzanie danych na brzegu systemu. Do jednostki centralnej przesyłany jest wtedy tylko jeden sygnał, czyli informacja o wykryciu człowieka w polu widzenia kamery. Nie ma już potrzeby przesyłania obrazu do komputera centralnego.
Jak projektuje się zasilacze dla inteligentnych czujników?
Inteligentne czujniki wymagają dodatkowej jednostki obliczeniowej, czyli zazwyczaj mikrokontrolera. Jednakże dodanie nowych elementów oznacza, że potrzebujemy wyższego poboru prądu niż w tradycyjnym rozwiązaniu. Należy więc projektować układy zasilające, które potrafią dostarczyć większy prąd.
Przykład zasilania inteligentnego czujnika za pomocą przewodu 2-żyłowego
Interfejs SPoE pomaga w realizacji inteligentnych czujników, ponieważ w 2-żyłowym kablu można przenosić zarówno dane, jak i zasilanie. SPoE łączy więc w sobie komunikację dwużyłową (jak np. standard 4‑20 mA) z zasilaniem przez Ethernet (PoE), Takie przewody w wielu wypadkach są już częścią infrastruktury w fabryce, więc nie trzeba ich układać. Dzięki SPoE można przesyłać moc do 52 W na odległość 400 metrów lub do 20 W na odległość do 1 kilometra. Napięcie zasilania wynosi 24 V lub 55 V. Transmisja danych oparta jest na standardzie 10BASE-T1L.
Rysunek 1 przedstawia schemat przykładowej implementacji SPoE za pomocą przewodu dwużyłowego oraz układów LTC4396-1 PSE (źródła) i LTC9111 PD (odbiornika zasilania).
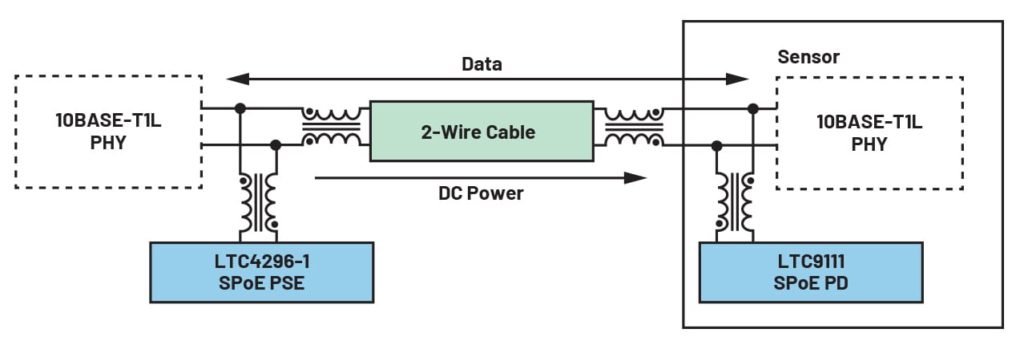
Rysunek 1. Przykładowa implementacja SPoE dla inteligentnych czujników
Energooszczędne czujniki w środowiskach przemysłowych
W środowisku przemysłowym często występują czujniki, które wymagają małej mocy zasilania. Dobrym przykładem mogą być czujniki wibracyjne, które rejestrują drgania maszyny. Badając drgania na odpowiednich częstotliwościach można sprawdzić czy wszystkie elementy pracują prawidłowo i nie wykazują oznak starzenia się. Dzięki temu można przewidzieć nieplanowaną awarię lub wykroczenie poza określoną tolerancję. Monitorowanie danych dotyczących wibracji wymaga stosunkowo zaawansowanych algorytmów, które przetwarzają duże ilości danych w czasie rzeczywistym. Te obliczenia mogą odbywać się lokalnie, przy każdej obserwowanej maszynie, lub też w jednym centrum danych.
W wielu zastosowaniach korzystne jest wykonywanie analizy danych lokalnie, blisko obserwowanej maszyny. Aby wykonać taką realizację, istniejące zakłady przemysłowe można po prostu wyposażyć w czujniki drgań – nie ma potrzeby układania dodatkowych kabli. Jeśli sensor wykryje sygnał sugerujący awarię lub inną nieprawidłowość wyśle określony sygnał ostrzegawczy.
Czujniki tego typu można przymocować magnetycznie do maszyny i dostarczać dane bezprzewodowo. Bardzo wygodna przy tym jest sieć typu mesh. W takiej sieci sensory komunikują się między sobą i przesyłają informacje do serwera, działając w pewnym stopniu jako repeatery. Dzięki temu zakład przemysłowy można łatwo wyposażyć w funkcje konserwacji predykcyjnej.
Jednym z przykładów jest technologia inteligentnego czujnika silnika OtoSense (ang. Smart Motor Sensor – SMS) firmy Analog Devices. Jest to kompletne, oparte o sztuczną inteligencję rozwiązanie do monitorowania stanu urządzenia, złożone z części sprzętowej oraz programowej. OtoSense monitoruje stan silników elektrycznych, łącząc najnowocześniejsze technologie czujnikowe z analizą danych opartą o AI.
Istotnym warunkiem funkcjonowania systemu są odpowiednie źródła zasilania dla czujników. Inteligentny sensor musi mieć moc nie tylko do zasilania elementu czujnikowego, ale także mikrokontrolera i (ewentualnego) układu radiowego. System projektuje się jednak tak, aby pobór energii był jak najmniejszy.
Źródłem energii może być bateria lub układ typu Energy Harvesting pozyskujący energię z otoczenia. Często zdarza się też, że obie metody są stosowane łącznie, dzięki czemu nie trzeba tak często wymieniać akumulatora.
Energię można pozyskiwać z różnych źródeł. W zależności od lokalizacji czujnika można zastosować ogniwa słoneczne, generatory termoelektryczne lub przetworniki piezoelektryczne. W zakładach przemysłowych często występują gradienty temperatury, które można przekształcić w energię elektryczną za pomocą generatorów termoelektrycznych opartych o efekt Seebecka. Również drgania mechaniczne można przekształcić w energię elektryczną za pomocą układów piezoelektrycznych.
W przypadku urządzeń zasilanych zarówno z baterii, jak i z układów pozyskiwania energii, kluczową rolę odgrywa efektywna konwersja napięcia. Aby ją osiągnąć, można wykorzystać jeden z kilku układów scalonych wyspecjalizowanych do zarządzania małą mocą.
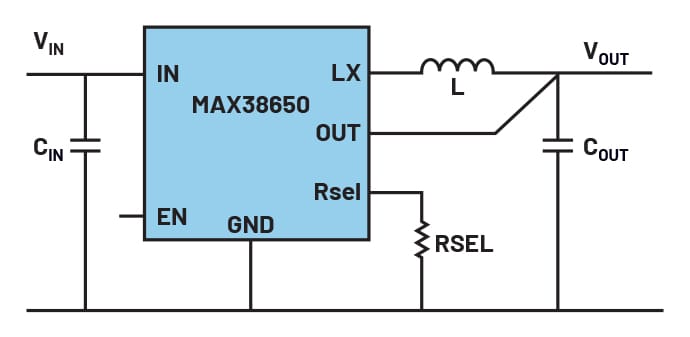
Rysunek 2. Konwersja napięcia dla sensorów zasilanych bateryjnie
Rysunek 2 pokazuje przykładowy układ konwersji napięcia za pomocą układu MAX38650. Jest to zasilacz impulsowy step-down pracujący przy prądzie do 100 mA. Może pracować z napięciem wejściowym do 5,5 V i dostarczać napięcie wyjściowe od 1,2 V do 5 V. Podczas pracy układ pobiera prąd spoczynkowy jedynie 390 nA (wartość typowa). Natomiast przy wyłączonym konwerterze, układ pobiera zaledwie 5 nA. W przypadku systemów konserwacji predykcyjnej dane z czujników zazwyczaj są pobierane co jakiś czas, a komunikacja z serwerem jest konieczna tylko w przypadku wystąpienia usterki. Oznacza to, że MAX38650 można bardzo często przełączać w tryb obniżonego poboru mocy, aby uzyskać dodatkowe oszczędności energii.
Większość konwerterów napięcia ma wyprowadzenie sprzężenia zwrotnego. Zazwyczaj podłącza się do niego dzielnik rezystorowy, za pomocą którego ustala się napięcie wyjściowe układu. Jednak taki dzielnik nie ma większego sensu, kiedy wyjątkowo zależy nam na oszczędności energii. Zazwyczaj bowiem przepływa przez niego zbyt duży prąd. Natomiast kiedy wartości rezystorów są duże, to wyprowadzenie sprzężenia zwrotnego widzi bardzo dużą impedancję, co może powodować przedostawanie się szumów i wpływać na prawidłową stabilizację napięcia wyjściowego. Zakłócenia szumami są szczególnie dotkliwym problemem w zakładach przemysłowych.
Jak pokazano na rysunku 2, układ MAX38650 ma pin RSEL. Działa on jednak w nieco inny sposób niż zwykle – napięcie wyjściowe ustalane jest przy pomocy tylko jednego rezystora. Po włączeniu układu MAX38650, przez ten zewnętrzny opornik przez krótki czas przepływa prąd rzędu 200 µA. Powstałe w ten sposób napięcie ustala napięcie wyjściowe na cały okres pracy przetwornicy. Jest to interesujące wyjście z sytuacji, gdyż pozwala połączyć niski prąd upływowy i solidną stabilizację napięcia wyjściowego.
Zasilacze dla sensorów małosygnałowych
Istnieją czujniki, które muszą mierzyć bardzo małe sygnały. Aby zapobiegać zniekształceniom takich pomiarów, zasilacz musi cechować się niskim poziomem szumów. Duży wpływ na to ma ograniczenie zakłóceń, zarówno przewodzonych, jak i promieniowanych. Te pierwsze można znacznie zredukować za pomocą filtrów wejściowych i wyjściowych. W przypadku źródeł promieniowanych nie jest to takie proste. Jednym z rozwiązań jest szczegółowe i dokładne zaprojektowanie płytki PCB, jednak nawet wtedy w systemie mogą indukować się szumy tła. Można je wyeliminować jedynie poprzez dobre ekranowanie, czyli zastosowanie metalowej obudowy, ale taka osłona jest czasochłonna i kosztowna w produkcji.
Konwerter impulsowy z technologią Silent Switcher® to rozwiązanie w bardzo sprytny sposób minimalizujące emitowane zakłócenia. W tym układzie ścieżki prądu impulsowego w zasilaczu zaprojektowano symetrycznie. Dzięki temu powstające pola magnetyczne w dużym stopniu znoszą się. Technologia ta, w połączeniu z technologią flip chip, która eliminuje połączenia drutowe pomiędzy krzemem a wyprowadzeniami obudowy układu scalonego, radykalnie zmniejsza wpływ zakłóceń promieniowanych na pracę systemu. Dzięki tym technikom możliwa jest redukcja zakłóceń promieniowanych aż o 40 dB.
Rysunek 3 przedstawia konstrukcję technologii Silent Switcher, w której dzięki symetrycznemu rozmieszczeniu ścieżek prądy impulsowe powstają jednocześnie, co pokazano na zielono. Prądy te wytwarzają pola magnetyczne o różnej polaryzacji i w rezultacie w większości znoszą się one wzajemnie.
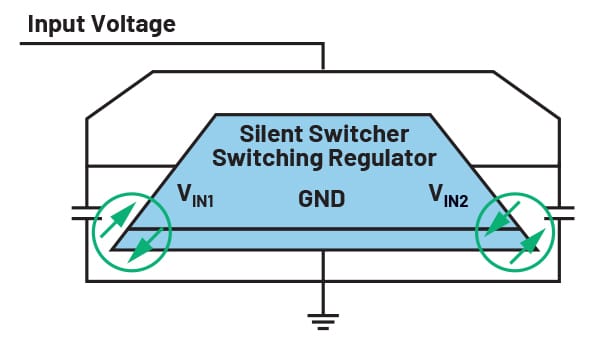
Rysunek 3. Minimalizacja zakłóceń promieniowanych w układach Silent Switcher
Obecnie mamy do czynienia z trzecią generacją Silent Switcher. Wprowadzono w niej kilka ulepszeń względem poprzednich wersji. Zastosowano m.in. specjalną technologię minimalizacji poziomu szumów na niskich częstotliwościach (10 Hz – 100 kHz). Pozwala to pominąć stabilizator LDO, który bywa stosowany jako filtr wyjściowy pomiędzy konwerterem impulsowym, a wrażliwym obciążeniem wyjścia.
Konwertery SIMO – kilka napięć wyjściowych na jednej cewce
Niektóre czujniki inteligentne muszą być umieszczone w bardzo małych obudowach — zwłaszcza kiedy nowy czujnik trzeba włożyć do obudowy po starym. Nowy układ ma o wiele bogatszą funkcjonalność, co oznacza, że ma też więcej elementów (jak mikrokontroler, układ radiowy itp.). W związku z tym należy przemyśleć sprawę miniaturyzacji niektórych elementów sensora, w tym również układów zasilania.
Ciekawym przykładem konwertera napięcia jest układ SIMO (ang. single-inductor multiple-output), który umożliwia generowanie kilku różnych napięć wyjściowych w układzie z tylko jedną cewką indukcyjną. Można w ten sposób zaoszczędzić miejsce na płytce PCB, które w innej topologii byłoby zajęte przez kilka cewek.
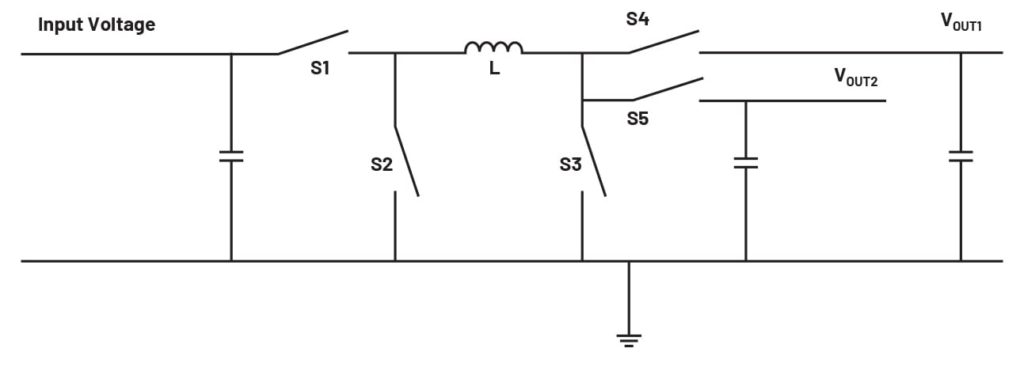
Rysunek 4. Zasilacz SIMO idealny dla bardzo małych czujników
Rysunek 4 przedstawia przykład prostego obwodu konwertera SIMO dla dwóch napięć wyjściowych. Można łatwo rozwinąć układ o kolejne wyjścia zasilania i nadal potrzebna jest tylko jedna cewka indukcyjna.
Zasilacze SIMO działają w następujący sposób: pojedyncza cewka indukcyjna jest używana kolejno dla wszystkich napięć wyjściowych. Cewka jest ładowana do pewnego poziomu wymaganego do wytworzenia napięcia VOUT1. Następnie cewka oddaje energię do pierwszego obciążenia i z powrotem ładuje się ją, aby była w stanie wytworzyć napięcie VOUT2. Ten cykl można powtarzać kilkukrotnie, w zależności od liczby wyprowadzonych napięć wyjściowych.
Podsumowanie
Artykuł skupia się na nowoczesnych czujnikach przemysłowych, które stają się coraz bardziej inteligentne. Oznacza to, że dane przez nie mierzone poddawane są wstępnej analizie już w układach sensora. Takie podejście rodzi wyzwania, również w obszarze zasilania urządzeń. Przedstawione w artykule przykłady to próba odpowiedzi na częste problemy z projektowaniem nowoczesnych zasilaczy dla tychże czujników.