Trochę chemii w elektronice, czyli mycie płytek krzemowych – według Grzegorza Kamińskiego
Już kilka razy wspominałem w moich tekstach o myciu płytek krzemowych w technologii wytwarzania przyrządów półprzewodnikowych. Ten proces jest wielokrotnie powtarzany w procesie technologicznym. W poprzednim tekście o fotolitografii napisałem, że każdy etap kończy się usunięciem fotorezystu i myciem płytek półprzewodnikowych. Generalnie proces mycia powtarza się w całym procesie technologicznym tak często jak proces fotolitografii. Przytoczę tu fragment tekstu z poprzedniego artykułu: “Wg. moich danych i na podstawie informacji z TSMC, dla technologii CMOS 350-110 nm wymaganych jest ok. 20 procesów fotolitografii. W technologiach z tego zakresu wykonuje się układy analogowe BiCMOS, gdzie w jednym układzie scalonym są układy bipolarne i CMOS. W takim przypadku liczba fotolitografii może wynieść nawet 30.“ Oznacza to, że również 20-30 razy wykonuje się proces mycia płytek półprzewodnikowych. Ogólny schemat przedstawia – prezentowany we wcześniejszej publikacji – rysunek poniżej:
Jak z niego wynika, fotolitografia i proces mycia płytek to najczęściej powtarzający się proces w technologii wytwarzania chipów podzespołów półprzewodnikowych. Z fotolitografii nie możemy zrezygnować bo to jest niezbędny etap by wytworzyć wszystkie elementy np. układu scalonego.
Dlaczego tak często myje się płytki półprzewodnikowe w cyklu technologicznym?
Jak dalej wyjaśnię, to wcale nie jest taki banalny, jakby się wydawało, proces. Czy można go pominąć, aby przyspieszyć produkcję lub uzyskać dodatkowe oszczędności? Niestety nie. Według statystyk aż 80% defektów, powstałych na etapie wytwarzania chipów podzespołów półprzewodnikowych, pochodzi od różnego rodzaju zanieczyszczeń. Między innymi dlatego procesy technologiczne wykonuje się w pomieszczeniach czystych, tzw. cleanroom’ach.
Przy wytwarzaniu urządzeń elektronicznych, a mam na myśli montaż podzespołów na płytkach PCB, jak coś pójdzie nie tak, np. złe polutowane, to możemy to skorygować. W produkcji chipów układów scalonych takiej opcji nie mamy. Każdy błąd czy defekt w strukturze chipu jest nie do naprawienia. Oczywiście, zdarzają się takie defekty, które nie skutkują niepoprawnym działaniem chipu lub jego parametrami niezgodnymi ze specyfikacją. Jednakże zwykle ma to wpływ na jakość i niezawodność.
Procentowy uzysk chipów na płytce o średnicy 200 mm
W produkcji podzespołów półprzewodnikowych, takich jak układy scalone czy elementy dyskretne, mamy do czynienia z pojęciem uzysku ( ang. yield). Uzysk wyrażany jest w procentach. Jest to stosunek liczby dobrych chipów po zakończeniu wszystkich procesów technologicznych, do liczby wszystkich chipów na płytce półprzewodnikowej. Załóżmy, że mamy płytkę o średnicy 8”, czyli 200 mm, a chip jest kwadratem o boku 2,5 mm . Wtedy jego powierzchnia wyniesie 6,25 mm2. Dla porządku dodam, że te 2,5 mm jest brane pod uwagę razem z linią cięcia, ponieważ jednym z pierwszych procesów tzw. back-end jest pocięcie płytki na poszczególne chipy. Efektywna powierzchnia płytki o średnicy 200 mm, na której są całe chipy, to ok. 29 864 mm2. Czyli wszystkich podzespołów na takiej płytce jest 4778 sztuk. Gdy uzysk wyniesie przykładowo 85%, to dobrych, w pełni funkcjonalnych i spełniających wszystkie wymagania chipów będzie 4061 sztuk. W produkcji podzespołów półprzewodnikowych uzysk nigdy nie osiąga 100%. W przypadku prostszych technologii jest on większy, a w bardziej skomplikowanych i z większą liczbą operacji oczywiście mniejszy. Zainteresowanych tematem uzysku, jego modelowania i kontroli procesu technologicznego, odsyłam do podręcznika “Fundamentals of Semiconductor Manufacturing and Process Control – G.May, C.Spanos”, wydawnictwa John Wiley & Sons z 2006 roku.
Trochę się o tym rozpisałem, ale to bardzo ważne by zrozumieć, że w produkcji chipów dążymy do maksymalizacji uzysku, a w tym może nam pomóc właśnie mycie płytek krzemowych. Pominięcie tego etapu nie wpłynie na przyspieszenie procesu z jednoczesnym obniżeniem kosztów. Wręcz przeciwnie, spadnie mam uzysk, a tym samym wydajność wytwarzania chipów. Wzrośnie też koszt jednostkowy chipu, jak pokazuje praktyka i statystyki.
Zanieczyszczenia na powierzchni płytek krzemowych
Można je podzielić na cząstki stałe, chemikalia oraz powłoki (błony lub warstwy nie wytworzone specjalnie w procesie technologicznym).
Cząstki stałe to takie, które mają określone krawędzie/granice. Zaliczamy do nich kurz, kłaczki z odzieży, ludzką skórę, bakterie z wody dejonizowanej (DI) itp.
Chemikalia mogą przybrać formę cząstek stałych lub powłok/błon na powierzchni płytki krzemowej. Błony z chemikaliów organicznych to np. pozostałości fotorezystu czy pot lub inne wydzieliny ludzkie po dotknięciu płytki gołą ręką. Zanieczyszczenia chemiczne to także jony metali. Szczególnie często literatura mówi o jonach potasu czy sodu, które wpływają na niestabilność napięcia progowego tranzystorów MOS. Często w procesie mycia płytek krzemowych stosuje się także procesy trawienia tlenków powierzchniowych.
Urządzenia do mycia płytek
Standardowe urządzenia do mycia płytek to ręczne, pół-automatyczne lub automatyczne systemy składające się z wielu “wanien” w których znajdują się chemikalia myjące. Przykładowe urządzenia firmy Modutek Corp. znajdują się na zdjęciu poniżej:
Na lewym zdjęciu widać koszyk (ang. carrier) z płytkami krzemowymi. Systemy automatyczne mają nawet do 20 “wanien” i koszyk jest przenoszony z jednej wanny do następnej automatycznie dzięki zastosowaniu odpowiedniego manipulatora.
Jak widać, procesowi mycia poddawany jest cały lot produkcyjny, czyli jeden koszyk zawierający zwykle 25 płytek. Są także inne systemy, gdzie jeden lub 2 koszyki ładuje się do komory roboczej przez drzwi, podobne do drzwi pralki automatycznej. Przykład takiego urządzenia francuskiej firmy Siconnex na kolejnym zdjęciu.
Po lewej widzimy urządzenie pół-automatyczne, do którego wkłada się ręcznie koszyk lub koszyki z płytkami półprzewodnikowymi, przez drzwi podobne do tych w pralce automatycznej. Po prawej stronie mamy urządzenie automatyczne, gdzie koszyki z płytkami przekłada automatycznie do takich samych urządzeń robot przemysłowy. Całość składa się z modułów.
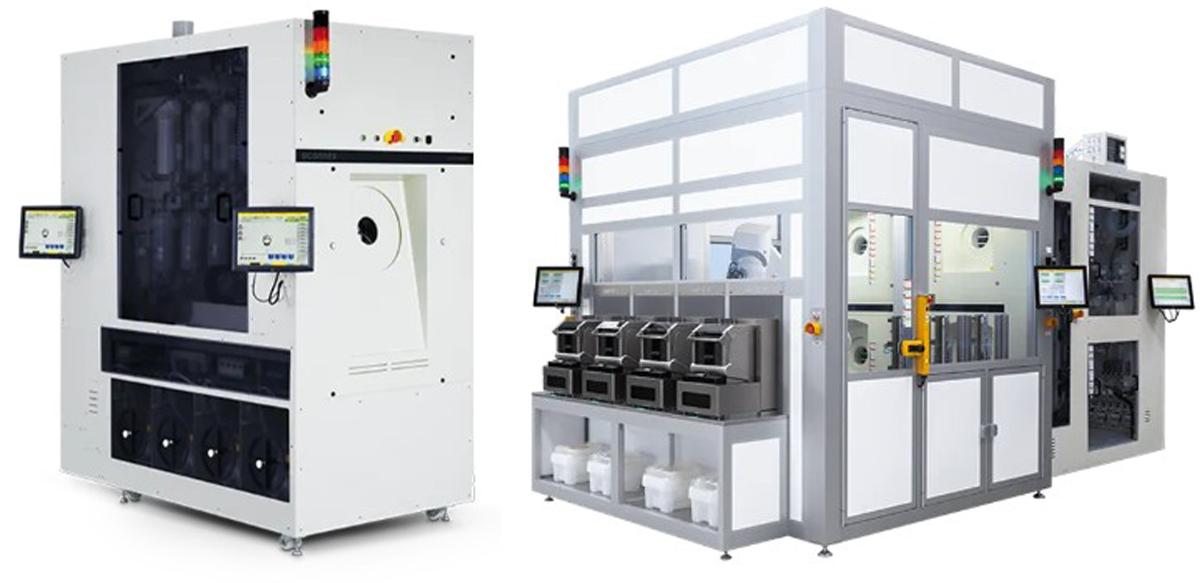
Rys.3: Urządzenia do mycia płytek krzemowych firmy Siconnex, po prawej wersje automatyczne, wielomodułowe
Nowoczesne systemy dla płytek 12” = 300 mm są to najczęściej systemy mycia pojedynczych płytek, automatycznie pobierane z koszyków transportowych.
Przykład takiego urządzenia na kolejnym zdjęciu. Jest to urządzenie jednego z największych producentów urządzeń do produkcji przyrządów półprzewodnikowych, japońskiej firmy TEL (Tokyo Elektron Ltd.). Urządzenia takie mają nawet 20 komór myjących, czyli można mieć 20 etapów mycia i wydajność do 650 umytych płytek na godzinę.
Przykładowa sekwencja mycia płytek krzemowych:
- H2SO4 + H2O2: usuwanie związków organicznych i zanieczyszczeń metalicznych;
- płukanie w wodzie dejonizowanej;
- HF/H2O: usunięcie naturalnych tlenków krzemu;
- płukanie w wodzie dejonizowanej;
- NH4OH + H2O2 + H2O: usuwanie cząstek stałych;
- płukanie w wodzie dejonizowanej;
- HF/H2O: usunięcie naturalnych tlenków krzemu;
- płukanie w wodzie dejonizowanej;
- HCl + H2O2 + H2O: usuwanie zanieczyszczeń metalicznych;
- płukanie w wodzie dejonizowanej;
- HF/H2O: usunięcie naturalnych tlenków krzemu;
- płukanie w wodzie dejonizowanej;
- suszenie.
Jak widać, ta sekwencja ma aż 13 etapów. Teraz podam kilka ciekawostek o używanych powyżej chemikaliach.
H2SO4 + H2O2 to mieszanina, która ma kilka nazw. Najbardziej popularna to pirania (ang. Piranha), ponieważ podczas mycia zachodzi reakcja odwracalna typu:
H2SO4 + H2O2 ⇌ H2SO5 + H2O
Powstały kwas nadtleno jednosiarkowy (ang. peroxymono sulfuric acid) zwany jest też kwasem Caro, od nazwiska niemieckiego chemika Heinricha Caro. Tak więc piranię nazywa się także mieszaniną Caro. Zwykle ma ona inne proporcje niż klasyczna pirania. Po zmieszaniu wody utlenionej z kwasem siarkowym szybko zachodzi reakcja egzotermiczna, czyli wydziela się duża ilość ciepła. Mieszanina, zależnie od proporcji, osiąga temperaturę od 110 do nawet 180 °C.
Niebezpieczne mieszaniny
Już w 1970 roku dwóch pracowników firmy RCA (Radio Corporation of America), panowie Werner Kern i David Puotinen, opracowali dwie mieszaniny myjące stosowane do dziś, nazywane SC-1 i SC-2 (SC – standard cleaner). Czasami od nazwy firmy używa się akronimów RCA-1 i RCA-2.
Mieszanina SC-1: NH4OH + H2O2 + H2O. NH4OH to tzw. woda amoniakalna, czyli roztwór amoniaku NH3 w wodzie. Chemicy powiedzą, że taki związek chemiczny jak NH4OH, czyli wg. prawidłowej nomenklatury wodorotlenek amonu, nie istnieje, ale powszechnie w literaturze tak się tę substancję opisuje.
Mieszanina SC-2: HCl + H2O2 + H2O a HCl to oczywiście kwas solny.
Nie będę opisywał tych związków i proporcji mieszanin, bo obecnie są stosowane różne ich odmiany. Dodam tylko, że woda utleniona H2O2 jest silnym utleniaczem i powoduje pomiędzy tymi chemikaliami także reakcję egzotermiczną, gdzie temperatura roztworów sięga powyżej 70 °C. Spadek temperatury jest dobrym wskaźnikiem, że związek zaczyna się rozkładać i zwiększa się ilość wody w mieszanie. Gdy temperatura jest za niska to skuteczność mycia spada.
Wszystkie wymienione wyżej mieszaniny, używane w procesie mycia, są niezwykle czyste pod względem chemicznym i tylko takie mogą być stosowane w przemyśle półprzewodnikowym
W opisanych wyżej procesach stosuje się duże ilości wody dejonizowanej ( ang. DI water). Jej czystość określa się poprzez mierzenie rezystywności. W temperaturze 25 °C rezystywność wody używanej w produkcji chipów powinna być lepsza niż 18 M𝛺-cm. Dla porównania, woda destylowana ma rezystywność 0.5 M𝛺-cm, a woda pitna ma tylko 0.01 M𝛺-cm. Mówiąc wprost, woda DI to chemicznie czyste H₂O.
Powyżej wspomniałem o kwasie fluorowodorowym HF. Służy on do trawienia tlenku krzemu SiO₂. Oczywiście proces ten musimy stosować tak, by nie usunąć tlenków, które specjalnie wytworzyliśmy, pełniących ważną rolę w przyrządzie półprzewodnikowym, np. tlenku bramki w tranzystorze MOS. I tutaj chciałbym zadać pytanie czy jest możliwe zanieczyszczenie płytek krzemowych przez sam proces mycia, zakładając, że wszystkie chemikalia są odpowiedniej jakości. Oczywiście, że tak. Zjawisko to po angielsku nazywa się “recontamination”. Właśnie dobrym przykładem jest wspomniany kwas fluorowodorowy. Jony fluoru tworzą z krzemem silnie wiązania. Większość fluoru możemy usunąć w procesie płukania wodą DI, ale aby proces ten był w 100% skuteczny, to woda DI powinna mieć ok. 80 °C.
Wszystkie wymienione substancje są niebezpieczne i należy się z nimi obchodzić bardzo ostrożnie, tym bardziej, że są to kwasy, które same się podgrzewają w trakcie zachodzących reakcji chemicznych. Przykładowo kwas fluorowodorowy powoduje bardzo trudno gojące się oparzenia. Na zdjęciu poniżej wygląd ręki po kontakcie z HF:
Dodatkowo fluor bardzo chętnie wchodzi w reakcję z wapniem, co dodatkowo powoduje uszkodzenia kości. Reakcja z wapniem jest też pewnym zbawieniem, bo żele na bazie wapnia są remedium na widoczne powyżej oparzenia po kontakcie skóry z tym kwasem.
Sam miałem niebezpieczną przygodę z kwasem fluorowodorowym. Jeszcze pracując w Fabryce Półprzewodników “Tewa” chciałem szybko usunąć tlenek z fragmentu płytki testowej i zanurzyłem ją w stężonym kwasie fluorowodorowym. W ciągu sekund rękawiczka, którą miałem na ręce, tylko od oparów tego kwasu, zaczęła się topić. Musiałem szybko opłukać rękę w dużej ilości wody. Na szczęście nic się poważnego nie stało. To zdarzenie miało jeszcze jeden zabawny efekt. Od tego momentu przestałem nosić obrączkę, by nie uległa uszkodzeniu od chemikaliów.
Mam nadzieję, że wyjaśniłem, jak ważne jest mycie płytek półprzewodnikowych w procesie wytwarzania diod, tranzystorów czy układów scalonych, i że nie jest to taki banalny proces.
To co napisałem to tylko podstawy. Jest bogata literatura na ten temat, a jednen z ekspertów w tej dziedzinie to prof. Jerzy Rużyłło, emerytowany profesor Pennsylvania State University i współautor monografii na ten temat liczącej ponad 600 stron – “Cleaning Technology in Semiconductor Device Manufacturing” 4th edition 1996 (ISBN 1-56677-115-3). Tutaj się pochwalę, że prof. Jerzy Rużyłło był promotorem mojej pracy magisterskiej, gdy jeszcze pracował na Politechnice Warszawskiej.