Trendy przyszłości w Przemyśle 4.0
Nie ma wątpliwości, że Przemysł 4.0 będzie miał ogromny wpływ na produkcję przemysłową, a wraz z rozwojem technik i technologii wpływ ten będzie się rozszerzał w sposób, którego jeszcze nie potrafimy przewidzieć.
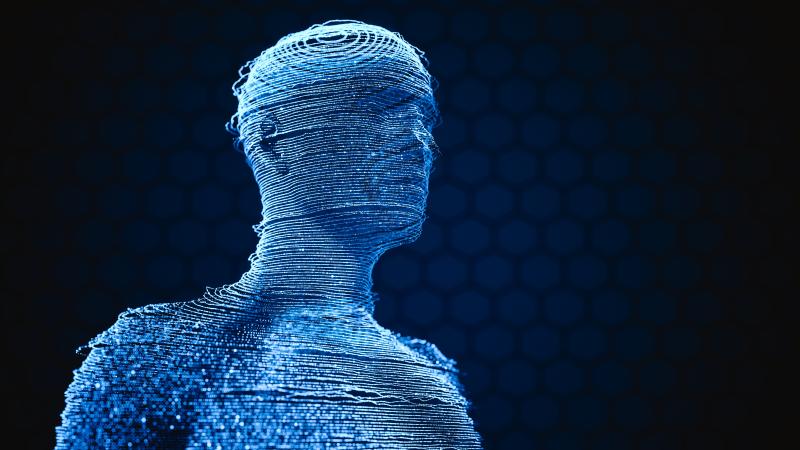
Jednak zaczynając od początku — czym dokładnie jest Przemysł 4.0?
Termin „Przemysł 4.0” odnosi się do wykorzystania technologii cyfrowych i automatyzacji w celu zmiany wydajności zakładów produkcyjnych. Opierając się na trzech podstawowych nurtach — automatyzacji, technologiach danych oraz integracji maszyn, oprogramowania i ludzi — Przemysł 4.0 ułatwia optymalizację produkcji, lepsze wykorzystanie zasobów oraz zwiększenie wydajności pracy. Jest to przede wszystkim płynna interakcja między oprogramowaniem, sprzętem i ludźmi, mająca na celu poprawę szybkości a także niezawodności przepływu informacji między systemami producenta, a ludźmi, którzy je obsługują.
Matt Dentino, Industrial IoT Channel Manager w Farnell, partner Advantech North America, zachwyca się korzyściami, jakie może przynieść technologia Przemysłu 4.0. „Przemysł 4.0 to integracja wielu technologii w przestrzeni przemysłowej. Integrując istotne dane w czasie rzeczywistym i przekazując je bezpośrednio przełożonm najwyższego szczebla, a teraz także do chmury, wyznaczamy nowe trendy. Przemysł 4.0 obejmuje dane przekazywane z maszyny do maszyny, kluczowe wskaźniki wydajności oraz rozszerzony wgląd, który zapewnia znacznie ściślejszą integrację operacyjną. Integracja może przebiegać na różne sposoby, ale w Advantech postrzegamy Przemysł 4.0 jako integrację, zaczynając od hali produkcyjnej, a kończąc na osobach podejmujących najważniejsze decyzje.”
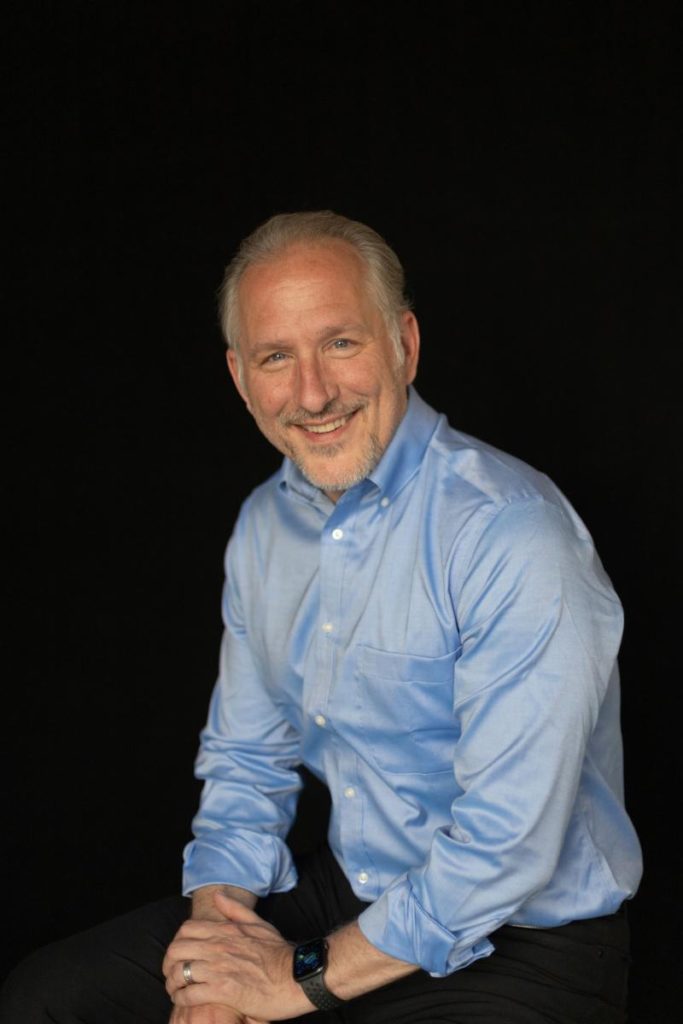
Jakie są główne trendy w Przemyśle 4.0?
Szybka łączność
Wraz z „eksplozją” danych pochodzących z rozmaitych maszyn i urządzeń, metody łączności będą musiały zostać dostosowane do obsługi rosnącego ruchu. Systemy i rozwiązania, które generują ogromne strumienie danych, takie jak drony, kamery wideo z funkcją samorozpoznawania i urządzenia rzeczywistości rozszerzonej wymagają łączności co najmniej 5G. W zależności od zastosowań, oczekuje się, że w najbliższych latach 5G będzie odgrywać główną rolę w rozwoju Internetu rzeczy (IoT).
Jest ku temu dobry powód. Do zalet 5G należą: większa szybkość sieci, mniejsze opóźnienia, ulepszona obsługa pozwalająca na podłączenie większej liczby urządzeń, mniejsze zużycie energii oraz segmentacja sieci, dzięki której firmy produkcyjne będą miały własną, bezpieczną sieć z gwarantowaną jakością usług (QoS). Podział sieci umożliwia różnym strefom w fabryce pracę z różnymi prędkościami i opóźnieniami, dzięki czemu administratorzy mogą przenieść cenną przepustowość z systemów niekrytycznych do obszarów, w których ilość danych jest większa.
Rzeczywistość rozszerzona
W środowisku produkcyjnym czas ma kluczowe znaczenie — zwłaszcza gdy urządzenia są wyłączone lub nie pracują z powodu konserwacji lub awarii — szybki dostęp do informacji o konserwacji jest niezbędny. Inżynierowie czy operatorzy procesów korzystają z rzeczywistości rozszerzonej, która oferuje więcej wiedzy w formatach, które ludzie mogą łatwo zrozumieć i wykorzystać. Umożliwia im to podejmowanie lepszych i szybszych decyzji w oparciu o fakty oraz twarde dane.
Matt Dentino z Advantech mówi: „Myślę, że technologia rozszerzonej rzeczywistości — która już istnieje w metawersum i w grach — przeniesie się do przestrzeni produkcyjnej. Już teraz lekarze szkolą się przy użyciu zestawów słuchawkowych i rękawic haptycznych, aby mogli wykonywać operacje i rozwijać umiejętności w warunkach rzeczywistości rozszerzonej — na długo zanim staną nad żywym pacjentem w prawdziwej sali operacyjnej.”
Łatwiejsze i szybsze kodowanie
Jedną z potrzeb rozwoju Przemysłu 4.0 jest uwzględnienie zmieniających się umiejętności współczesnych pracowników. Starsi inżynierowie odchodzą na emeryturę zabierając ze sobą swoje umiejętności. Umiejętności te mogą obejmować bardziej tradycyjne podejście do programowania. Oznacza to, że potrzebne są prostsze sposoby programowania urządzeń i systemów, które uwzględniają fakt, że nowi pracownicy są „cyfrowymi tubylcami”.
„Ważnym aspektem jest platforma aplikacji o niskim poziomie kodowania, co sprawiło, że wielu inżynierów oprogramowania podkreśla potrzebę zapoznania się z tą technologią i możliwościami” — mówi Matt Dentino.
„Tam, gdzie wcześniej opracowanie procedury automatyzacji z wykorzystaniem logiki drabinkowej i prawidłowe ustawienie programów na linii zajmowało kilka tygodni, teraz może to zająć kilka minut dzięki technologii konfiguracji oraz metodologii „przeciągnij i upuść”. Oznacza to, że nawet jeśli starsze umiejętności zanikają wśród pracowników, będziemy obserwować szybsze przyjmowanie zautomatyzowanych procesów, ponieważ część kodowania, która tradycyjnie zajmowała najwięcej czasu, może być teraz wykonana automatycznie znacznie szybciej bez specjalistycznej wiedzy, która była wcześniej wymagana.”
Sztuczna inteligencja
Sztuczna inteligencja jest wykorzystywana w produkcji w wielu zastosowaniach Przemysłu 4.0, w tym do gromadzenia i analizowania danych na potrzeby konserwacji predykcyjnej, uczeniu maszynowym w celu optymalizacji procesów, a tym samym poprawy jakości, zwiększenia wydajności i oszczędności energii oraz w optymalizacji czy śledzeniu produkcji w czasie rzeczywistym. Można ją również wykorzystać do szkolenia nowych pracowników, uczących się od doświadczonych operatorów i inżynierów firmy, którzy przekazują je podczas sesji szkoleniowych w rzeczywistości wirtualnej lub rozszerzonej.
Alexandra Rangel, National PowerXpert Application Engineer w dziale komponentów energetycznych w Eaton, partnera Farnell. „Myślę, że zobaczymy o wiele więcej SI” — mówi.
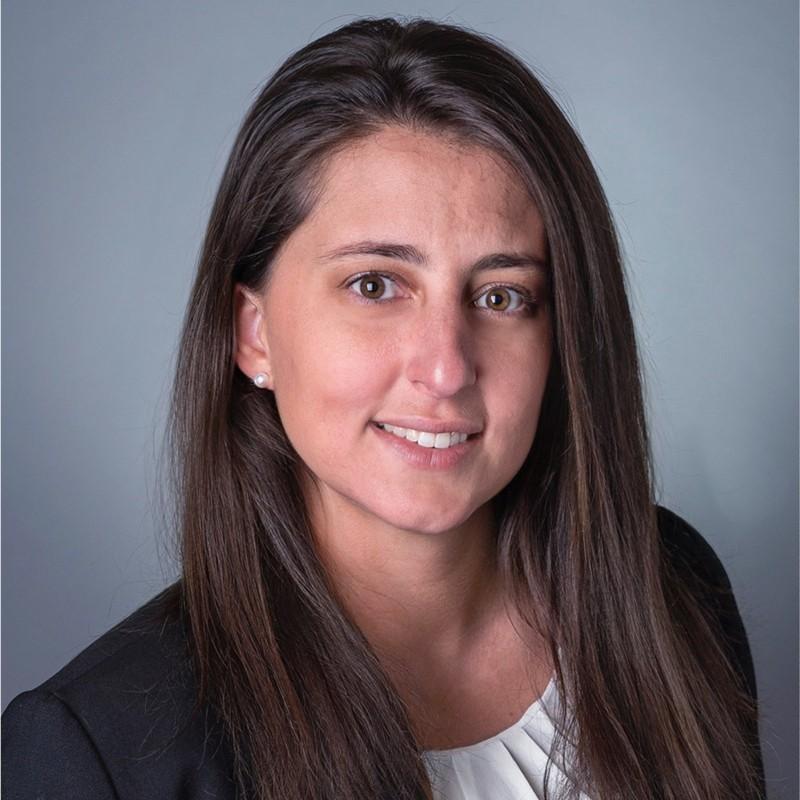
„Duże korporacje, takie jak Eaton, przeznaczają znaczne ilości środków na zatrudnianie ekspertów od analizy danych. Sztuczna inteligencja, w której można wykorzystać te dane nie tylko pozwoli maszynie na ustalenie, co jest potrzebne i przedstawienie opcji, ale także na podjęcie świadomej decyzji, doprowadzając do większej autonomii w zakładach produkcyjnych.”
Autonomia, o której mówi Alexandra Rangel, skróci czas potrzebny na podjęcie decyzji o usprawnieniach oraz realizację zadań wymaganych do optymalizacji procesów. Rezultatem będzie mniejsza ilość odpadów, szybsza reakcja na zdarzenia i lepsza ogólna jakość wynikająca z bardziej precyzyjnych procesów.
Barry Turner, Technical Business Development Manager w Red Lion Controls, podkreśla elastyczność, jaką zapewni SI. „Klienci Red Lion na pewno korzystają z SI” — mówi Barry Turner.
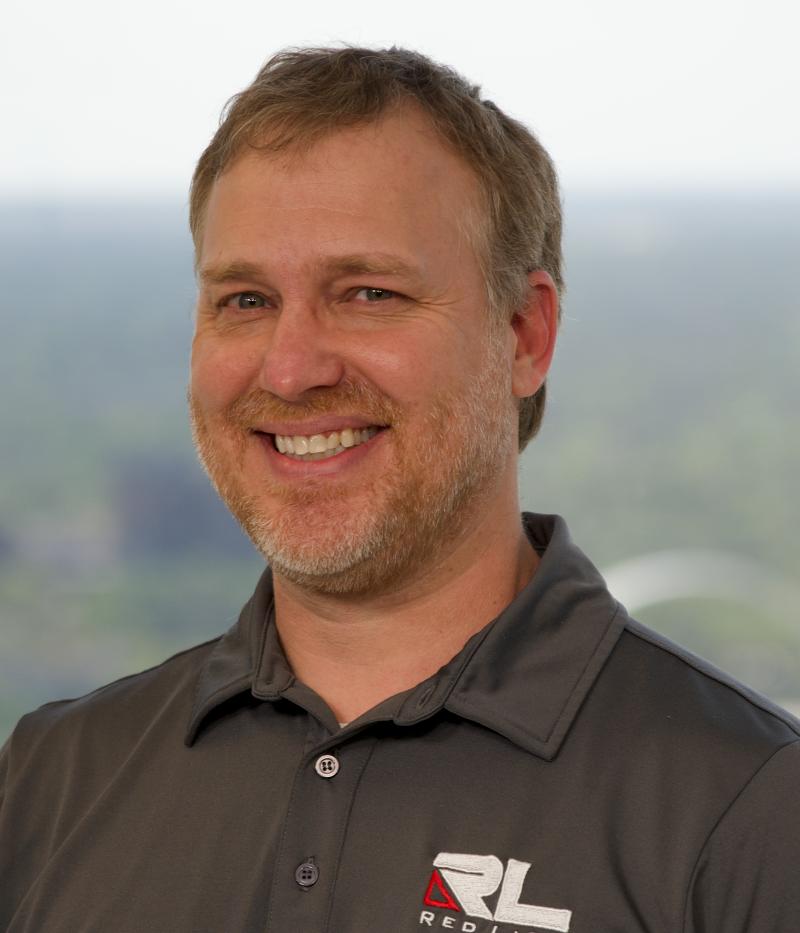
„Nasze produkty mogą komunikować się praktycznie ze wszystkim, wyciągając dane, agregując je, a następnie wysyłając gdziekolwiek trzeba, w tym do chmury. Oznacza to, że klienci korzystający z FlexEdge od Red Lion, naszych interfejsów HMI i innych produktów wspierających nasze oprogramowanie Crimson mogą pobierać dane z czegokolwiek w zakładzie, przetwarzać je przy użyciu inteligencji obliczeniowej urządzeń brzegowych, a następnie wysyłać te informacje do chmury. Chmura może zrobić z tymi danymi wszystko, czego potrzebujesz, w tym wykorzystać sztuczną inteligencję lub uczenie maszynowe do analizy efektywności istniejących procesów lub zaproponować nowe sposoby działania.”
Lepsza integracja danych OT i IT
Kolejnym trendem jest zbliżanie się do siebie tradycyjnie odrębnych dziedzin technologii operacyjnej (OT) i technologii informacyjnej (IT). Systemy OT monitorują zdarzenia, procesy i urządzenia oraz wprowadzają korekty w operacjach przedsiębiorstw czy przemysłu, podczas gdy systemy IT są wykorzystywane do przetwarzania danych.
Przemysł 4.0 wywołuje konwergencję maszyn mechanicznych, urządzeń elektromechanicznych i innego sprzętu przemysłowego z nowszym, cyfrowym światem serwerów, pamięci masowych oraz sieci. Przy odpowiednim wdrożeniu konwergencja IT/OT prowadzi do połączenia procesów biznesowych, wglądu i kontroli w jeden w pełni skoordynowany, jednolity system.
Barry Turner z Red Lion, dodaje: „Myślę, że największą zmianą będzie przyspieszenie i adaptacja. Gdy więcej osób zrozumie, że Przemysł 4.0 polega na łączeniu danych OT z danymi IT w celu poprawy wyników biznesowych, będziemy w stanie rozwiązać wiele problemów związanych z dzisiejszym łańcuchem dostaw.
„Znajdziemy sposoby na wykorzystanie danych z OT, połączenie ich z danymi z IT i stworzenie lepszych modeli biznesowych. Poza tym, w końcu przejdziemy do Przemysłu 5.0. Podczas gdy Przemysł 4.0 polega na jak najlepszej dodatkowej wartości z naszych aplikacji przemysłowych, Przemysł 5.0 – na ponownym wykorzystaniu tej wartości i ponownym jej zainwestowaniu.”
Podsumowanie
Konieczność zaspokajania coraz bardziej zróżnicowanych potrzeb klientów, konkurowania zarówno pod względem jakości, jak i ceny, zwiększania wydajności, ograniczania zużycia energii oraz radzenia sobie z coraz bardziej nieprzewidywalnym środowiskiem biznesowym oznacza, że producenci z różnych branż muszą być bardziej elastyczni i szybciej reagować, jeśli chcą odnieść sukces w przyszłości, jaką jest Przemysł 4.0.