Rozwój fabryk dzięki automatyce
W naszym świecie ma miejsce znaczny postęp w sposobie wytwarzania i produkcji towarów. Ten okres przemian nazywamy czwartą rewolucją przemysłową, czyli Przemysłem 4.0. Przemysł 4.0 uwzględnia trendy automatyzacji i wymiany danych w technologiach oraz praktykach produkcji, które obejmują sztuczną inteligencję (AI), przetwarzanie brzegowe i łączność.
Omówione tutaj trendy są niezwykle przyszłościowe, wręcz futurystyczne, dlatego wiele firm zwyczajnie nie jest jeszcze na nie gotowych. Rozumiemy, że firmy znajdują się na różnych etapach tej pełnej przemian drogi, ale wszyscy prędzej czy później uczestniczyli w pierwszej rewolucji przemysłowej (czyli zastosowali maszyny z napędem parowym), następnie w drugiej rewolucji „technologicznej” (kolej i telegraf) i wreszcie trzeciej (cyfrowej). Tak samo teraz przewidujemy, że z czasem wiele nowych dzisiaj trendów rewolucji przemysłowej zwyczajnie się upowszechni.
Widząc podwójnie
Aby sprostać rosnącemu globalnemu popytowi oraz wyzwaniom związanym z łańcuchem dostaw, producenci muszą myśleć przyszłościowo. Istnieje na to nowy, opłacalny sposób, który polega na stworzeniu tzw. cyfrowego bliźniaka, czyli wirtualnego obrazu danego fizycznego systemu lub procesu w czasie rzeczywistym, który służy jako cyfrowy odpowiednik do symulacji, integracji, testów i konserwacji. Cyfrowe bliźniaki pozwalają na szczegółowe symulacje działania sprzętu obejmujące wszystko – od procesów produkcyjnych po całe układy hal fabrycznych.
Budując wirtualnie maszynę, linię produkcyjną lub magazyn, firma nie musi wydawać pieniędzy na części ani sprzęt, a cyfrowy bliźniak pozwala sprawdzić, czy planowana inwestycja będzie działać jeszcze przed jej rzeczywistą realizacją. Cyfrowy bliźniak może utwierdzić twórców w przekonaniu, jak zbudować dany system, a gdy fabryka już fizycznie powstanie, można go wykorzystać do prac nad sprawnością i konserwacją predykcyjną.
Na przykład w magazynie Digi-Key możemy skorzystać z naszego cyfrowego bliźniaka, aby sprawdzić ile stanowisk pakowania należy uruchomić podczas kompletacji zamówień, a zależnie od ich liczby zamówień możemy określić, czy obsadzić je większą liczbą pracowników czy też przeciwnie – ograniczyć załogę. Cyfrowy bliźniak może również ułatwić określenie liczby zamówień, którymi możemy zarządzać w oparciu o wahania poziomu obsady, co z kolei pozwala określić optymalne rozwiązanie.
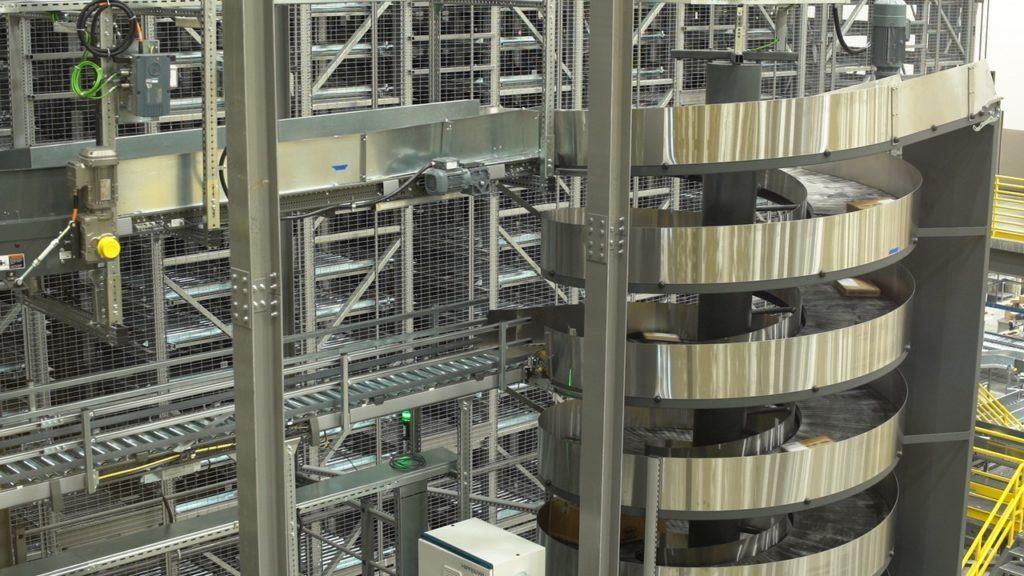
Korzyści ze stosowania cyfrowego bliźniaka
Kolejna korzyść dotyczy konserwacji predykcyjnej i doskonalenia procesów. Dzięki wirtualnej symulacji obiektu produkcyjnego firmy mogą cyfrowo modyfikować swoje projekty i sprawdzić, w jaki sposób usuwać problemy, bądź zidentyfikować bolączki i mankamenty. Każdy komponent w fabryce ma swój okres eksploatacji. Po pewnym czasie więc silniki i części nieuchronnie zaczynają szwankować i zawodzić pod względem elektrycznym. Dzięki cyfrowemu bliźniakowi uruchomionemu na platformach konserwacji predykcyjnej system może generować alarmy mówiące na przykład: „Uwaga! Ten silnik przepracował już X godzin. Właśnie zaczyna generować widoczne drgania. Taki poziom drgań oznacza, że awaria silnika nastąpi za trzy tygodnie, jeden dzień i dwie godziny od teraz”. Dzięki temu można proaktywnie zaplanować przestój w celu wymiany silnika zamiast reagować dopiero na niespodziewaną awarię, która wywoła załamanie całego systemu.
Korzystanie z cyfrowego bliźniaka umożliwia firmom wirtualne obserwowanie przyszłościowych rozwiązań przed wdrożeniem ich w świecie rzeczywistym. Cyfrowy bliźniak może również na przykład przyspieszyć prace i wykonać badania zwykle zajmujące tydzień w zaledwie godzinę, a zatem jego potencjał jest niesamowity.
Przetwarzanie brzegowe
Największym przejawem postępu technologicznego, który umożliwił stosowanie cyfrowych bliźniaków, jest przetwarzanie brzegowe, dzięki któremu wszystkie obliczenia można wykonywać z dużą szybkością. W miarę powszechnego wzrostu mocy obliczeniowych praktyki te staną się coraz częściej spotykane. Obecnie koszty systemów do obsługi przetwarzania brzegowego są dość wysokie, a zatem nieosiągalne dla wielu organizacji. Jednak korzyść w postaci dokładnego prognozowania zapotrzebowania kadrowego oraz świadomość konieczności wymiany systemów jest nieoceniona dla operatorów fabryk. Zapewnia to oszczędność czasu, a operatorzy, zamiast planować konserwacje, dokładnie wiedzą, kiedy nastąpi awaria systemu i mogą jej zapobiec, skracając czas przestoju linii.
Zastosowanie technologii przetwarzania brzegowego i cyfrowych bliźniaków stwarza ponadto więcej wysokopłatnych i zorientowanych na technologię miejsc pracy, np. dla informatyków, analityków danych, itp. Możemy do tego dodać roboty współpracujące ze sobą w halach fabrycznych, które są w stanie przejąć więcej nużących i powtarzalnych prac, a tym samym odciążyć pracowników, którzy je wcześniej wykonywali oraz pozwolić im objąć bardziej prestiżowe stanowiska w firmie.
Przedstawienie musi trwać
Niezależnie od tego, czy chodzi o problemy z maszynami, braki komponentów, czy inne potencjalne wyzwania, przestoje w produkcji nie wchodzą w grę. Dzisiejsze fabryki wymagają widoczności całego systemu dzięki zastosowaniu złożonych czujników i sprzętu zaprojektowanego do przechwytywania, monitorowania i dostarczania kluczowych informacji zanim pojawią się kłopoty.
Największy problem, z jakim zmagają się współczesne zakłady, to brak dosłownie miliona wykwalifikowanych pracowników z branży automatyki. A o poprawie tej sytuacji nie ma co marzyć. Dlatego wyzwanie polega na znalezieniu procesów, które należy zautomatyzować, aby pracować z tą samą liczbą osób, ale przy tym się rozwijać. Automatyka jest skalowalna – kiedy coś zautomatyzujemy, zwykle możemy wykonywać czynności, angażując w nie mniejszą liczbę osób lub nie musimy zatrudniać więcej pracowników w miarę rozwoju firmy.
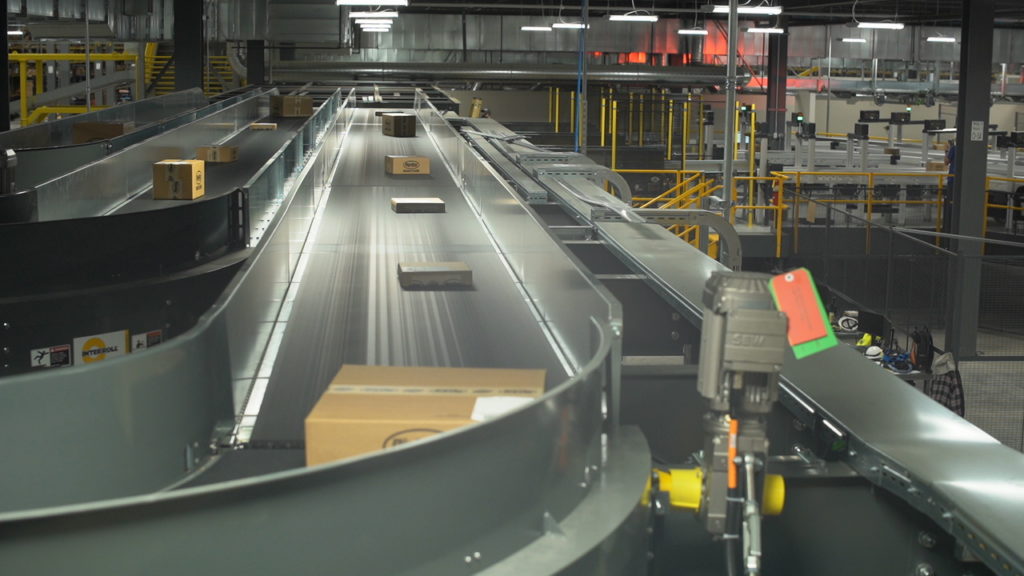
Pandemia pogłębiła ten trend, ponieważ firmy dość szybko zorientowały się, że prawdopodobnie nigdy nie będą mogły zatrudnić wystarczającej liczby pracowników, aby zaspokoić popyt. Wyzwanie polegało na ustaleniu, co można zautomatyzować i co tak naprawdę oszczędza pieniądze. Zwykła zamiana żywego pracownika na robota niekoniecznie stanowi rozwiązanie i eliminuje potrzebę zatrudnienia tej osoby.
Istnieje również wielkie zapotrzebowanie na integratorów systemów, którzy pomagają producentom zdecydować, co można zautomatyzować i w jaki sposób zapewnić bezproblemową współpracę wszystkich elementów. Dlatego studenci zdecydowanie powinni uczyć się automatyki i dowiedzieć się, w jaki sposób zdobyć zatrudnienie na stanowisku integratora, ponieważ wtedy będą gotowi do pracy w przyszłości.
Wychodzenie poza schematy
Pionierzy w świecie produkcji zawsze myślą perspektywicznie i tworzą prototypy przyszłych technologii dla hal fabrycznych. Patrząc przyszłościowo, wystąpi wiele trendów krótkoterminowych, które przeniosą Przemysł 4.0 ze świata idei do rzeczywistości.
Zapotrzebowanie na integratorów systemów będzie się utrzymywać i nadal będziemy notować większy nacisk na produkcję zlokalizowaną. Ten trend występuje nie tylko w Stanach Zjednoczonych, ale w skali globalnej: wszyscy pragniemy, aby nasza produkcja odbywała się bliżej docelowej lokalizacji produktu. Dobrze zlokalizowana produkcja ułatwia firmom dostarczanie produktów niestandardowych, projektów jednorazowych oraz mniejszych partii.
Zmierzając w stronę bardziej zautomatyzowanej przyszłości, firma Digi-Key stara się oferować wszystko, czego potrzebują klienci, aby przygotować się do kolejnej rewolucji we własnej firmie. Digi-Key posiada w magazynach 70 tysięcy części do automatyki i 150 tysięcy dostępnych produktów automatyki i sterowania, czyli prawie wszystko, czego można potrzebować do automatyzacji. Nie bez powodu jesteśmy ekspertami w dziedzinie automatyki.