IIoT i uczenie maszynowe kształtują przyszłość konserwacji predykcyjnej
W fabrykach, zakładach i innych obiektach przemysłowych, miliony maszyn rozwijają produkcję wszystkiego, czego potrzebujemy, od żywności i leków po samochody i komputery. Ale nawet najlepsze maszyny nie mogą działać wiecznie. Zużycie elementów zbiera swoje żniwo. Kiedy wewnętrzne usterki, takie jak zużycie łożysk, przegrzanie silników elektrycznych lub warunki zewnętrzne – wilgotność i temperatura, powodują uszkodzenia lub całkowitą awarię tych krytycznych zasobów, nawet na krótkie okresy, wpływ na organizacje może być poważny.
Na przykład dane z raportu Senseye Predictive Maintenance z 2022 r., platformy do zarządzania sprawnością maszyn opartej na sztucznej inteligencji firmy Siemens, sugerują, że przeciętny duży zakład traci 25 godzin miesięcznie na nieplanowane przestoje maszyn [1]. Według raportu, koszt pojedynczej godziny przestoju waha się od średnio 39 tys. USD, w przypadku fabryk produkujących szybko zbywalne dobra konsumpcyjne, do ponad 2 mln USD w sektorze motoryzacyjnym. Z kolei firma konsultingowa Deloitte twierdzi, że nieplanowane przestoje maszyn kosztują producentów przemysłowych około 50 mld USD rocznie [2].
Pobierz e-book
Takie statystyki oznaczają, że czekanie na awarię sprzętu lub maszyny przed jej naprawą nie jest opłacalną strategią konserwacji. Nie jest nią również naprawa lub wymiana bez rzeczywistej przyczyny. Odpowiedzią jest konserwacja predykcyjna.
Zapobieganie awariom maszyn
Konserwacja predykcyjna (tradycyjnie znana jako monitorowanie stanu) nie jest nową koncepcją. Jej początki sięgają co najmniej wczesnych lat 90. ubiegłego wieku. Jej celem jest uruchomienie serwisowania maszyny w momencie, gdy czynności konserwacyjne są najbardziej opłacalne, ale zanim wydajność sprzętu stanie się niezadowalająca. W praktyce, po osiągnięciu wyznaczonego progu stanu maszyny, podnoszony jest alarm, a inżynierowie dokładnie sprawdzają jej stan, aby zlokalizować usterki i naprawić je, zanim dojdzie do eskalacji.
Wartość tej metodologii jest znacząca. Deloitte twierdzi, że wdrożenie konserwacji predykcyjnej prowadzi do oszczędności kosztów materiałowych średnio od pięciu do 10 procent rocznie; od 10 do 20 procent wydłużenia czasu sprawności i dostępności sprzętu; od 5 do 10 procent obniżenia ogólnych kosztów konserwacji oraz od 20 do 50 procent skrócenia czasu planowania konserwacji. Według McKinsey Global Institute, konserwacja predykcyjna oparta na Przemysłowym Internecie Rzeczy (IIoT) zazwyczaj redukuje przestoje maszyn nawet o 50 procent i wydłuża ich żywotność nawet o 40 procent [3].
Korzyści płynące z konserwacji predykcyjnej nie ograniczają się do produkcji. Praktycznie każda branża, która polega na zasobach fizycznych w zakresie usług lub produkcji, może skorzystać z tej technologii. Przykładowo, przedsiębiorstwa użyteczności publicznej mogą wdrożyć narzędzia do konserwacji predykcyjnej i monitorowania, aby zapobiec kosztownym przerwom w dostawie energii, które w przeciwnym razie spowodowałyby ogromne zakłócenia.
IIoT usprawnia konserwację predykcyjną
We wczesnych latach konserwacji predykcyjnej, brak odpowiednich czujników do gromadzenia danych i ograniczone zasoby obliczeniowe do zestawiania i analizowania informacji utrudniały jej wdrożenie. Obecnie, ze względu na postępy w dziedzinie IIoT, przetwarzania w chmurze, analizy danych i uczenia maszynowego (ML), konserwacja predykcyjna jest powszechna zarówno wśród małych i średnich przedsiębiorstw (MŚP), jak i dużych firm. Około trzech czwartych respondentów raportu Siemensa uznało konserwację predykcyjną za priorytet strategiczny.
Solidne technologie bezprzewodowe o niskim poborze mocy, takie jak Bluetooth LE, zasilają czujniki, które gromadzą dane w sieciach setek, tysięcy lub dziesiątek tysięcy urządzeń. Czujniki IIoT monitorują parametry, takie jak temperatura i wibracje sprzętu, ciśnienie, poziomy gazu i zużycie energii, umożliwiając zespołom serwisowym uzyskanie lepszego wglądu w przewidywany przyszły stan sprzętu i wyprzedzające reagowanie na problemy przed ich wystąpieniem.
„Dane są paliwem dla każdego silnika konserwacji predykcyjnej. Ich jakość i ilość są czynnikami ograniczającymi analizę przyczyn źródłowych i przewidywanie awarii z dużym wyprzedzeniem” – czytamy w opracowaniu Deloitte poświęconym pozycjonowaniu predykcyjnego utrzymania ruchu. IIoT zapewnia ciągły strumień tego „paliwa”. Czujniki stale gromadzą dane, a następnie przesyłają krytyczne informacje z powrotem do centralnego serwera lub chmury w celu analizy za pośrednictwem bramy.
Sieci bezprzewodowe przynoszą inne korzyści. Umożliwiają na przykład monitorowanie zasobów w niebezpiecznych środowiskach i trudno dostępnych lokalizacjach, których ludzie powinni unikać. Sieci bezprzewodowe znacznie zmniejszają również koszty związane z instalacją, konserwacją i wydajnością systemów konserwacji predykcyjnej.
Uczenie maszynowe w akcji
Zbudowanie sieci bezprzewodowej, która może generować miliony punktów danych dziennie, każdego dnia, to jedno. Ale nadanie sensu tym wszystkim danym w odpowiednim czasie, aby zareagować na pojawiające się problemy, to zupełnie inna sprawa. Aby zminimalizować koszty i energię związaną z przesyłaniem dużych ilości danych (z których większość nie będzie godna uwagi), znaczna część obliczeń jest wykonywana w samej sieci przy użyciu techniki zwanej przetwarzaniem brzegowym. Wymaga to dużej mocy obliczeniowej i pamięci, fuzji czujników i, coraz częściej, uczenia maszynowego.
Fuzja czujników to proces łączenia danych z czujników w taki sposób, że uzyskane informacje mają mniejszą niepewność (tj. są bardziej precyzyjne lub kompletne) niż byłoby to możliwe, gdyby źródła czujników były używane indywidualnie. ML to zastosowanie sztucznej inteligencji (AI), które pozwala komputerom uczyć się bez bezpośredniego programowania lub instrukcji. Algorytmy ML uczą się na podstawie danych, a następnie uogólniają je na niewidoczne dane, a tym samym podejmują decyzje bez wyraźnych instrukcji. Rezultatem jest ciągłe zwiększanie możliwości maszyny i wysoki stopień autonomii.
Przetwarzanie brzegowe i fuzja czujników umożliwia urządzeniom IoT lokalne przesiewanie danych w celu podjęcia decyzji, które z nich są przyziemne, a które wskazują, że coś się zmienia i powinno zostać oznaczone. Poprzez dodanie uczenia maszynowego do miksu, urządzenia brzegowe wykraczają poza sprawdzanie danych w celu kontroli, czy przekroczyły one ustalone progi, do wnioskowania (wyciągania wniosków na temat przyszłego stanu czegoś z informacji już o nim znanych), co oznacza zmiana – a następnie coś z tym zrobić.
Jednym z przykładów związanych z konserwacją predykcyjną jest czujnik temperatury monitorujący łożysko maszyny. Czujnik mógłby wykorzystać model uczenia maszynowego, aby wywnioskować, że stopniowy wzrost temperatury łożyska to po prostu rozgrzewanie się maszyny i nie jest to powód do niepokoju. Jednak szybszy wzrost temperatury łożyska może wskazywać na awarię smarowania i spowodować wyłączenie maszyny przed wystąpieniem uszkodzeń mechanicznych.
Zasilanie analitycznego predykcyjnego utrzymania ruchu
Wiele z dzisiejszych zaawansowanych modeli ML wymaga znacznych zasobów obliczeniowych i wysokiego zużycia energii do przeprowadzania wnioskowania. Jednak ogromna liczba dzisiejszych urządzeń podłączonych do IoT, choć jest w stanie wykonywać pewne obliczenia brzegowe i fuzję czujników, nie ma dostępu do tych zasobów.
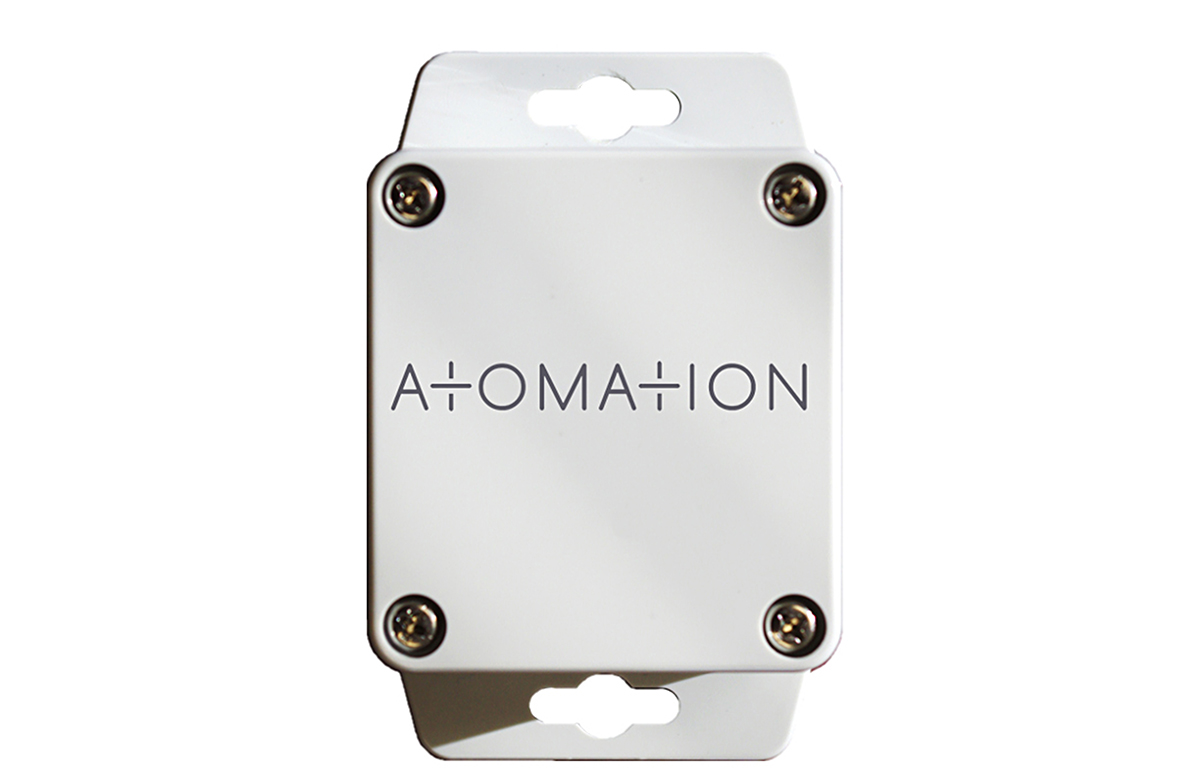
Atomation Atom — zasilany przez nRF52840 SoC firmy Nordic — monitoruje drgania, aby śledzić stan maszyny
Rozwiązaniem jest Tiny Machine Learning lub TinyML. Technologia ta jest podsektorem ML, który usprawnia oprogramowanie w taki sposób, że mogą go obsługiwać zasilane bateryjnie urządzenia wbudowane oparte na mikrokontrolerach, takie jak bezprzewodowe systemy w chipie (SoC).
Partner projektowy Nordic, Edge Impulse, dostarcza oprogramowanie TinyML do działania na układach SoC nRF52840, nRF5340 i najnowszym nRF54H20. Nordic dostarcza aplikację, która może być używana do trenowania i wdrażania wbudowanych modeli ML na platformie prototypowania Thingy:53 IoT firmy. Aplikacja umożliwia deweloperowi przesyłanie nieprzetworzonych danych z czujników za pośrednictwem urządzenia mobilnego do opartego na chmurze Edge Impulse Studio i wdrażanie w pełni wytrenowanych modeli ML do Nordic Thingy:53 przez Bluetooth LE.
Możliwości te doprowadziły do opracowania czujników takich jak Atomation Atom, zasilanych przez Nordic nRF52840 SoC. Czujnik mierzy oscylacje, aby określić, czy silnik maszyny wibruje bardziej niż wczoraj, lub monitoruje temperaturę, aby sprawdzić, czy łożysko jest gorące podczas pracy maszyny. Każdy Atom działa do trzech lat na baterii litowo-jonowej 3,6 V.
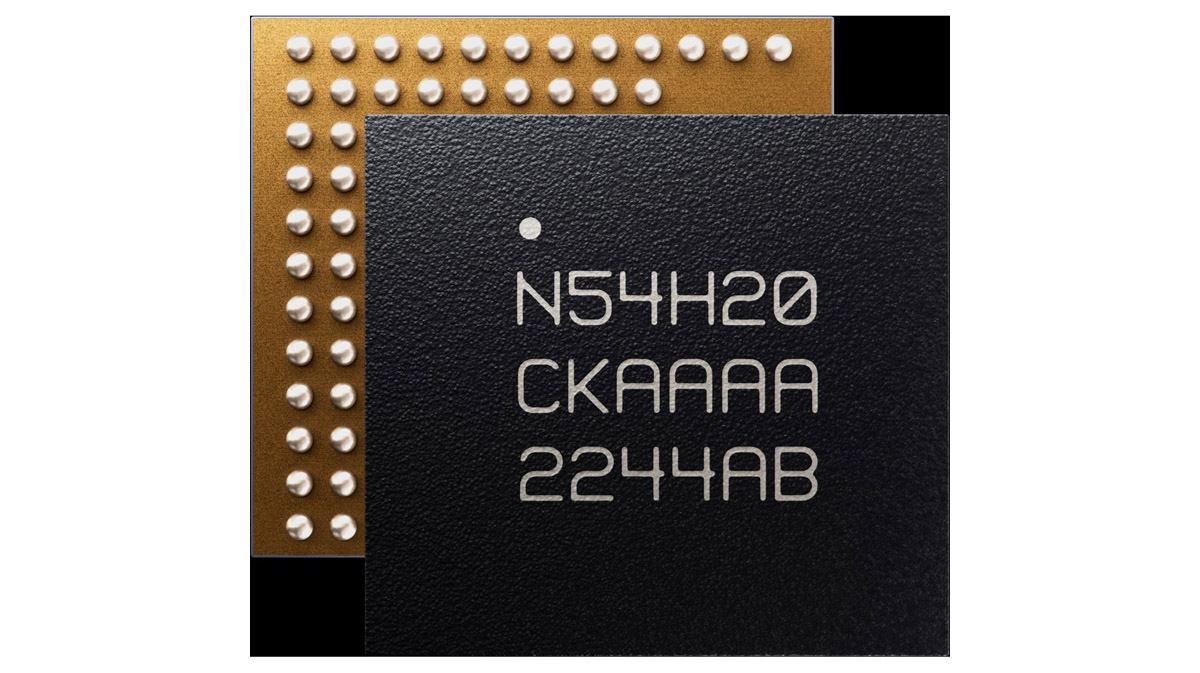
SoC nRF54H20 firmy Nordic obsługuje TinyML i zapewnia potężne zasoby obliczeniowe i pamięci dla aplikacji konserwacj
Czujniki monitorują i przetwarzają informacje lokalnie, zamiast wysyłać ciągły strumień danych z powrotem do centralnego systemu. Gdy progi zostaną przekroczone lub sprzęt działa poza normalnymi parametrami, dane są wysyłane do bramy za pośrednictwem łączności bezprzewodowej Bluetooth LE. Na przykład, urządzenia Atom mogą określić i odpowiedzieć na pytania takie jak: „czy urządzenie jest włączone czy wyłączone?”, „czy silnik wibruje bardziej niż wczoraj?” lub „czy temperatura łożyska jest zbyt wysoka, gdy maszyna pracuje?”.
– Nordic SoC jest prawdziwym „mózgiem” naszych Atomów, a mózg ten musi przyjmować surowe dane z czujników, konwertować je na użyteczne informacje i podejmować niezależne decyzje przed komunikacją w trudnym środowisku RF – wyjaśnia Steve Hassell, CEO w Atomation.
Co będzie dalej?
Konserwacja predykcyjna w coraz większym stopniu wykorzystuje zautomatyzowaną analitykę opartą na ML. Oznacza to jeszcze lepsze wyniki przy mniejszym zaangażowaniu człowieka. Zwiększa to jednak również zapotrzebowanie na moc obliczeniową na brzegu sieci. Firma Nordic przewidziała ten popyt dzięki nowej generacji układów SoC krótkiego zasięgu, serii nRF54.
Nowe układy SoC integrują wiele procesorów Arm Cortex-M33 i koprocesorów RISC-V, przy czym każdy procesor jest zoptymalizowany pod kątem określonego rodzaju obciążenia. W połączeniu z wbudowaną, nieulotną pamięcią o dużej pojemności i pamięcią RAM, nRF54H20 SoC wyposaża dewelopera w zwiększone zasoby obliczeniowe i pamięci potrzebne do uruchamiania złożonych aplikacji konserwacji predykcyjnej opartych na technologii ML. Co więcej, użycie nRF54H20 w połączeniu z układem scalonym do zarządzania energią (PMIC), takim jak nPM1300 firmy Nordic, skutkuje bardzo niskim zużyciem energii, wydłużając żywotność baterii, obniżając wymagania konserwacyjne i zmniejszając ilość odpadów.
Przyszłe rozwiązania konserwacji predykcyjnej, oparte na nowej generacji układów SoC, takich jak nRF54H20, będą jeszcze bardziej elastyczne, wydajne i zrównoważone. Umożliwi to operatorom wszystkich typów maszyn maksymalizację potencjału ich zasobów przy jednoczesnym wydłużeniu ich żywotności. Konserwacja predykcyjna przeszła długą drogę w ciągu zaledwie trzydziestu lat.
- „The True Cost of Downtime 2022”
- „Predictive Maintenance”
- „Produkcja: Analytics unleashes productivity and profitability”
Źródło: Nordic